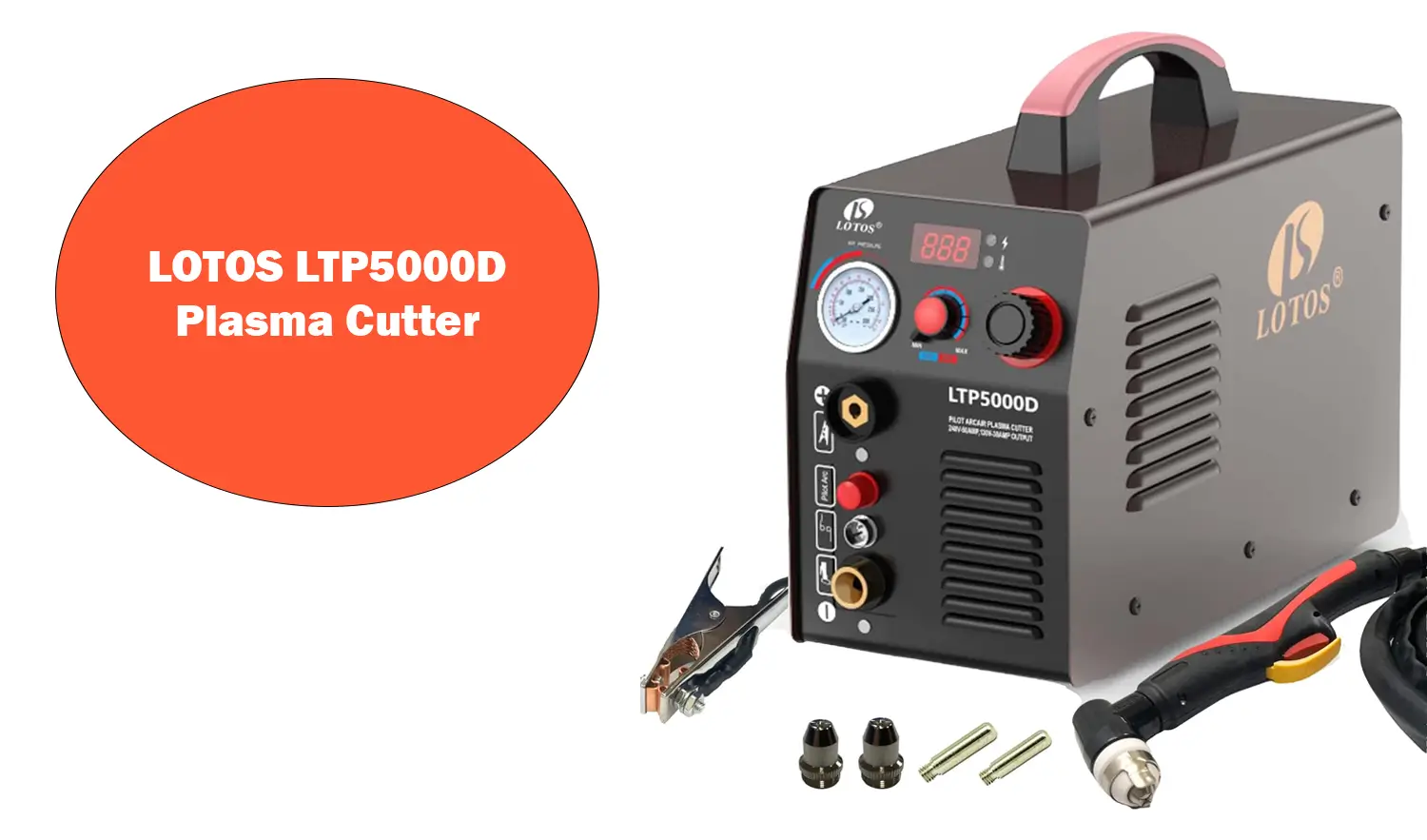
TIG welding, also called Gas Tungsten Arc Welding (GTAW), is a precise and versatile welding process renowned for producing high-quality welds across various metals, including stainless steel, aluminum, and exotic alloys. Here’s a detailed look into how TIG welding works and its key aspects:
TIG welding creates an arc between a non-consumable tungsten electrode and the workpiece. The electrode, typically made of pure or a tungsten alloy, is held in a specialized torch that allows precise control over the arc and shielding gas flow. This gas, often argon or a mixture of argon and helium, protects the weld area from atmospheric contamination, ensuring solid welds.
Arc Initiation: The welding begins with the tungsten electrode held close to the workpiece. When the electrode touches the metal, a high-frequency starting circuit creates an arc, which heats the metal to its melting point.
Arc Control: Once the arc is established, the welder manipulates the torch to control its intensity and movement. The distance between the electrode, the workpiece (arc length), and the welding speed is crucial for maintaining the heat input and achieving the desired weld characteristics.
Adding Filler Metal (if needed): In some TIG welding applications, a filler metal rod is manually counted to the weld pool to support the joint and provide additional material where necessary. This is common in thicker materials or when welding dissimilar metals.
Cooling and Solidification: As the weld progresses, the molten metal refrigerates and firms, forming a solid bond between the workpieces.
High Quality: TIG welding produces clean, precise welds with minimal spatter, making it suitable for critical aesthetics and strength applications.
Versatility: It can fuse various metals and thicknesses, from thin-gauge materials used in aerospace to thicker plates in industrial applications.
Control: Welders have excellent control over heat input, arc characteristics, and filler metal deposition, allowing for intricate welds and welding of complex joints.
TIG welding is widely used in industries such as:
Electrode Selection: Based on the material being welded and the welding current, choose the correct type and diameter of the tungsten electrode. Thoriated tungsten is standard for DC welding, while created or lanthanide tungsten suits AC welding.
Cleanliness: To prevent contamination, ensure the tungsten electrode and the workpiece are meticulously clean. Use a dedicated stainless steel wire brush to clean tungsten electrodes.
Arc Control: Maintain a consistent arc length (typically 1-3 electrode diameters) and control the torch angle to direct the heat precisely onto the weld joint without overheating or underheating.
Shielding Gas Flow: Set the shielding gas flow rate according to manufacturer recommendations to ensure adequate coverage and prevent the weld pool from oxidizing.
Practice Control: TIG welding requires steady hands and precise control of the torch movement. Practice controlling the filler rod addition and torch angle to achieve smooth weld beads.
Post-Weld Cleaning: After welding, clean the weld area thoroughly with a wire brush and solvent to remove any residue or oxidation that could affect the weld’s integrity.
Understanding its controls is crucial to effectively operate a TIG welding machine (GTAW). Here’s a breakdown of typical controls found on TIG welding machines:
Cleanliness: Ensure the tungsten electrode and workpiece are clean to prevent contamination and ensure quality welds.
Tungsten Electrode Selection: Based on the welded material and the welding current (DC or AC), choose the appropriate tungsten electrode type (pure tungsten, thoriated, created, etc.).
Electrode Grind: Grind the tungsten electrode to a fine point. The electrode diameter and grind angle affect arc stability and weld bead appearance.
Gas Selection: Depending on the material and welding conditions, pure argon or a helium-argon mix is used as the shielding gas.
High-Frequency Start: On modern machines, high-frequency starting circuits eliminate the need for physical contact between the tungsten electrode and the workpiece, reducing tungsten contamination.
Lift Arc Start: An alternative method where the tungsten electrode touches the workpiece briefly before lifting to initiate the arc. This method is standard in machines without high-frequency start.
Arc Length: To control heat input and arc stability, maintain a consistent arc length (typically 1-3 electrode diameters).
Torch Angle: Position the torch at the correct angle (usually 15-45 degrees) to effectively direct heat onto the weld joint.
Filler Metal Addition: Slowly feed the filler rod into the weld pool, controlling the puddle size and reinforcing the joint.
Cooling: Allow the welded area to cool naturally to avoid introducing stress or distortion.
Clean-up: After welding, clean the weld area with a wire brush and solvent to remove residual oxidation or contamination.
A1: TIG welding suits many metals, including stainless steel, aluminum, titanium, copper, nickel alloys, and more.
A2: TIG welding offers superior control over heat input, produces clean welds with minimal spatter, and allows for welding thin materials without distortion.
A3: TIG welding can be automated using robotic systems for consistent and high-volume production welding.
A4: Avoid touching the tungsten electrode to the molten weld pool or filler metal. Use a dedicated stainless steel wire brush to clean the electrode between welds.
A5: Wear appropriate personal protective equipment (PPE), including welding gloves, a welding helmet with a proper shade lens, and flame-resistant clothing. Ensure satisfactory ventilation in the welding site to prevent exposure to welding fumes.
TIG welding stands out for its precision, cleanliness, and versatility. It is preferred for demanding welding applications where quality and aesthetic considerations are paramount. By mastering the art of controlling the arc and manipulating filler metal, skilled TIG welders can achieve welds of exceptional strength and appearance across a broad spectrum of materials and industries.
At Best Welder Reviews, Hamim Minhas has years of welding experience and expertise in evaluating welding tools and accessories. My goal is to provide clear, reliable and deep insights to help welders of all levels make informed decisions. Whether you're a beginner or an expert, my thorough reviews, buying guides, and tips ensure you find the right tool for every welding project.
Copyright © 2025 Best Welder Review. All rights reserved.