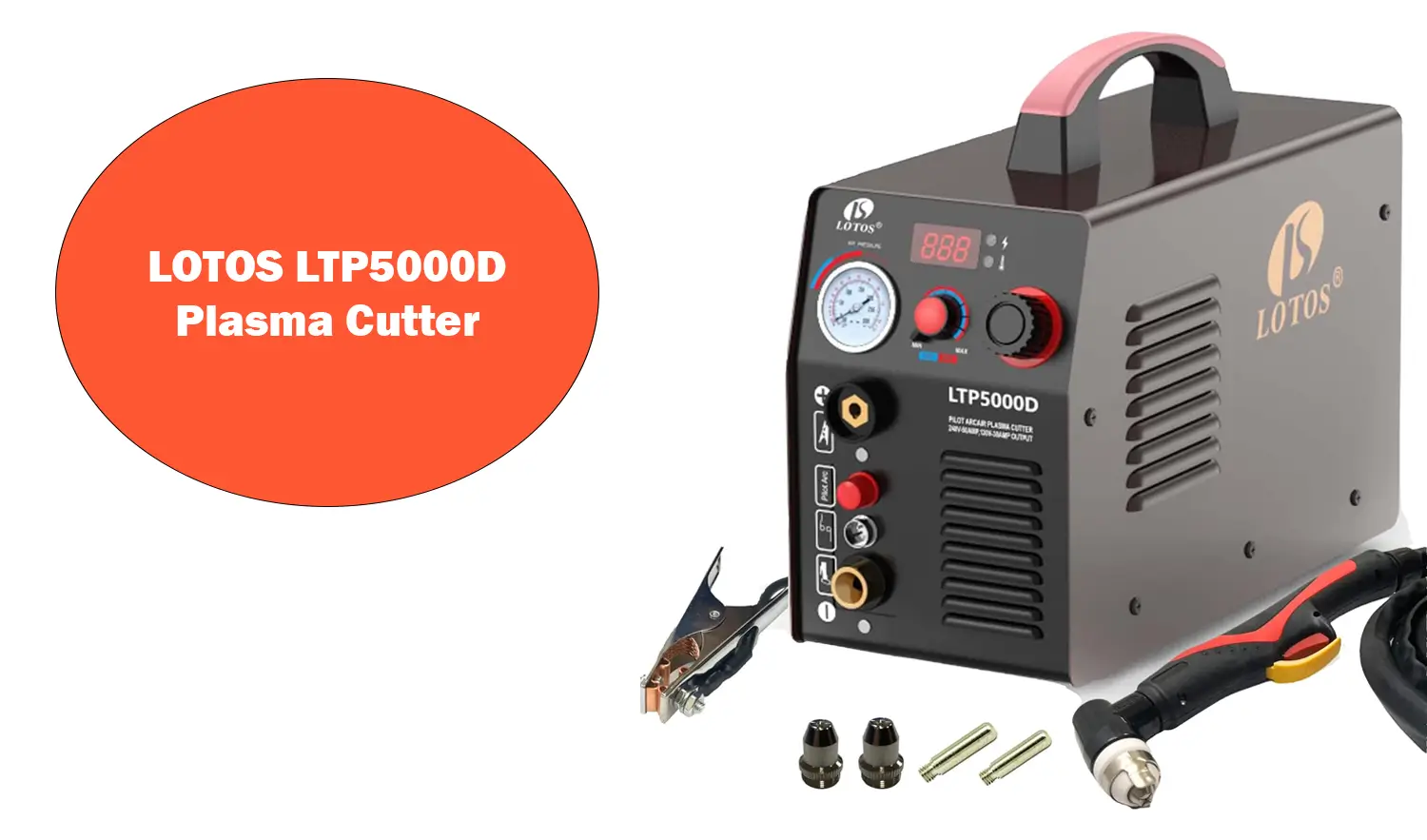
Welding is an essential part of manufacturing, construction, automotive, and other industries in which metals are joined.
The strength, durability, and quality of weld are crucial factors that directly affect the integrity of a final product. Start applying their own market-specific machines to connect specific applications, environments, and material properties.
These techniques are fundamental for every welder, from new to seasoned. Weld types, joint configurations, and selection factors are discussed, and the guide provides further insights into how to make the best weld decisions.
Butt Weld One of the most common and versatile types of welding is butt welds. This type of joint comprises two pieces of metal welded together end-to-end in the same plane.
This method is widely adopted in construction, pipelines, and automotive manufacturing industries. And butt weld, as they provide a strong and continuous joint with high integrity.
Butt welds can be either simple, but for thicker materials, beveled edges are typically employed to improve weld penetration and ensure a solid weld connection. Butt welds come in different types for different thicknesses or stress requirements, such as single V, double V, single U, and double U.
A fillet weld connects two metal surfaces at a right angle, like in T-joints, lap joints, and corner joints. This forms a triangular cross-section to distribute stress evenly, resulting in one of the most potent forms of welding.
Fillet welds are standard in structural applications, heavy machinery, shipbuilding, general fabrication, etc. This design option allows you to modify the size and shape of the fillet as needed and thus change the strength.
When made correctly, fillet welds can handle fatigue and loads very well; they make a tremendous, unobtrusive solution in highly stressed areas.
Groove welds have two elements of metal fitted within a groove to allow for deeper penetration of weld material. This is an essential type of weld on thicker materials where standard welding procedures must provide more strength.
Groove welds include V-groove, U-groove, J-groove, and bevel groove. Some factors that affect the selection of groove type are material thickness, welding position, and joint strength requirements.
Groove welds are used in pressure vessels, pipelines, and structural steel work due to the importance of achieving the maximum strength of the joint.
This involves welding through a hole (plug) or a slot in one piece of metal to attach to yet another piece. Commonly used to join overlapping materials, these welds provide a permanent bond that resists shear forces.
Examples of plug and slot welds include automotive body panels, sheet metal fabrication, and structural applications. Their shape, size, and spacing will dramatically determine how the welding is done, how strong that weld will be, and how the load will be distributed across that weld.
With these welds being done correctly, a strong, visually pleasing joint is created, which meshes with adjacent base materials.
Seam welding involves continuously welding two overlapping metal sheets, creating a tight leak proof join. This technique is often used to manufacture pipes, tubes, and containers that must be water-tight or air-tight.
Resistive welding techniques are typically used to avoid leakage seams, with electrodes driving the sheets together under pressure, promoting heat generation via electrical resistance, and welding the workpieces together.
This process produces consistently uniform welds with minimal distortion, making resistance welding well-suited for mass production in automotive, aerospace, and appliance manufacturing applications.
The success of seam welding depends mainly on how well the heat and pressure (from the electrodes) are controlled.
Spot welding is a fast process that can join two or more metal sheets at minor, localized points. It has broad utility in the automotive, furniture, and sheet metal manufacturing sectors.
The procedure clamps the sheets between two electrodes and runs a high current through them to create a small weld nugget. Spot welding works well in thin materials and has many automated places, which makes it great for high-volume production. However, due to the low penetration and typical strength, it is not recommended for thick or high-strength materials.
Edge welds connect the edges of two or more sheets of metal. It is helpful for thin materials where deep weld penetration is not required. Edge welds are commonly used in applications like edge reinforcement, flange welding, or sealing edges in sheet metal work.
This type of weld is excellent at adding material to worn or damaged parts, restoring the part to its former shape and function. Edge welds may lack the strength of butt or fillet welds.
Still, they provide sufficient strength for specific applications requiring appearance and low distortion type weldments.
Instead of joining two pieces of metal, surfacing welds add a material layer to a surface. It is commonly used to reconstitute fatigue in fatigued components, improve wear resistance, or provide protective corrosion-resistantcorrosion-resistant coatings.
The type of surfacing process used depends upon the material type and properties required. It may include MIG, TIG, and stick welding. The surface can be a dominant layer of a particular material — hardened, toughened, or chemically resistant.
Common in mining, construction, and manufacturing industries, surface welds extend the lifespan of critical components.
Flange welds are used when two materials abutting towards its edge must join along a flanged surface. The flange also increases the area available for welding, giving the joint additional strength and rigidity.
This weld is commonly utilized in piping systems, structural elements, and heavy gear. Flange welds can withstand bending and twisting forces, which is why they are used in high-stress applications.
Weld preparation and alignment of the flanges are critical to achieving a sound, uniform weld.
Projection welding is essentially the same as spot welding, except that instead of using unaltered/unconformed metal pieces, you would use preformed projections made to one (or both) of the work pieces to help concentrate conduction welding current.
It’s a process that forms several welds at once, thus increasing productivity and saving time.
Projection welding has widespread applications in manufacturing fasteners, nuts, bolts, and electrical components. Welds done this way are repeatable, strong, and need minimal cleanup.
Tack welding is the first step in the welding process, where small, temporary welds help to keep the pieces in place before the primary process begins.
They also correctly align and space the components, minimizing the potential for jagging and warping during welding. In complex assemblies, tack welding is valuable and maintains dimensional accuracy.
Though not expected to support loads, tack welds should be strong enough to withstand handling and positioning forces when fabricating.
Stitch welding is a seam welding technique that produces the weld in discrete, intermittent points along the joint. This method decreases the heat input and helps avoid warping and distortion with thin materials.
Stitch welds are often used in sheet metal work, automotive panels, and other situations where it is optional to weld the entire length of the seam. Stitches can have different spacing and lengths to balance strength, aesthetics, and thermal effects.
The most straightforward kind of joint is a butt joint in which two pieces abut one another edge-to-edge. They are used in everything from small fix-its to big structural projects.
This requires proper edge preparation, such as beveling, to achieve an appropriate penetration and weld strength. However, butt joints can be welded with multiple methods, including MIG, TIG, and stick welding.
If one piece of metal is perpendicular to another, making a T shape, this forms T-joints. These joints are typically found in structural frameworks, machinery, and automotive chassis. Depending on strength and load requirements, filter, plug, or slot welds can be used to weld T-joints. Ideally, they are positioned and heated to avoid defects such as warping and incomplete fusion.
In lap joints, two pieces of metal are overlapped and welded along the edge of the overlap. Dusting joints can be used in applications like sheet metal, car bodies, etc. In this type of joint, the lap distance can be increased depending on load-bearing. To make an intense & attractive weld, it is necessary to clean and align the weld properly.
Corner joints are formed when two metal pieces join at a right angle, creating a corner. It is also commonly used in enclosures, frames, and box construction. Fillet, butt, or edge welds can be used to weld corner joints according to the application and strength required.
Reinforcing Biometry-Deferring Illustration, March 2022Biometry-Deferring Illustration, January 2023It’s like a double fracture joint around the body.
In edge joints, two or more pieces of metal are placed together with the edges and welded along the edge. The 70-Degree Butt Joint — Although not the most common, butted joints are utilized in sheet metal work, where the material is relatively thin and deep penetration is not required.
Edge joints also can strengthen edges, join flanges, or seal edges of containers. Edge joints do not offer as strong a joint as some of the others we will see, but they are a good (and low-stress) means of joining two pieces together for specific situations.
The second type involves two flat plates crossing at their connected center at 90º, creating a cross-sectional shape known as cruciform joints. This type of joint is employed in heavy structures and applications that need a substantial load-bearing capacity.
The arrangement of weld penetration is similarly essential, as it can regularly adjust load tension to avoid stress concentrations and form a strong joint.
The flanged butt joint is a variation of the standard butt joint in which the edges of the pieces are flanged to give an additional surface to weld on. This joint increases strength and rigidity; thus, it is often used for high-stress applications such as pipelines and pressure vessels.
They resist bending and shear forces and are used when a durable joint is needed to prevent failure.
These are metal pieces joined at a right angle, forming a T shape. They are typically found in structural frames, pipelines, and mechanical assemblies. Depending on the type and thickness of the material and the application, tee joints can use fillet, groove, or plug welds for joining.
With the wire-arc additive manufacturing process complete, defects such as incomplete fusion or undercutting should be acceptable if done right and at the correct position.
The type of base material being welded greatly influences the kind of joint and weld to be used. Thus, metals react differently during welding due to their divergent thermal characteristics, melting points, and expansion.
Stainless steel needs to be carefully heat treated to prevent warping; aluminum is fussy in cleanliness and has high accuracy due to its oxidation nature.
Knowledge about the material properties determines the suitable welding process and weld joint design to achieve the desired results.
The load the weld and joint will be bearing is critical in the selection process. When high pressures or intense beams like a fillet weld or a groove weld are required, the welds are more potent than those required. On the flip side, simple welds such as edge or tack welds may be acceptable for less critical applications such as sheet metal enclosures.
Assessing the load requirements ensures the joint will be reliable under operating conditions.
Correctly preparing a joint is crucial for producing a good weld. This encompasses cleaning the metal surfaces of contaminants, beveling edges for greater penetration, and confirming proper alignment between the pieces.
Poor cleaning can ideal defects like porosity, incomplete fusion, and weak joints, compromising weld integrity. Joint preparation also makes things more manageable, improves weld quality, and reduces rework and failure rates.
Different welding positions, such as flat, horizontal, vertical, and overhead, affect the difficulty and quality of the weld. Certain types of welds are more readily available to perform in certain positions. In contrast, others may necessitate changes in technique or equipment. Overhead welding, for example, is more difficult because gravity causes the weld pool to sag.
Weld types and positions: Proper integration of the weld with the base metals helps create a clean and strong weld with limited objections.
Joint access is one of the determining factors of the welding process. Tight or confined places may require additional work to perform specific welding techniques or joint designs.
By approaching the joint design with accessibility in mind, the welding process can become easier to execute, with a lower chance of error and increased overall efficiency.
In applications where appearance is essential, such as automotive bodywork or decorative metalwork, the selected weld and joint type can affect the final appearance.
Imperfections such as open joints, excessive spatter, and rough finishes are often unwanted. Techniques such as TIG welding or fillet welds executed to perfection cannot only approach aesthetic perfection but also be structurally sound.
Different welding techniques differ in terms of the time and cost it takes to perform them. Weld types vary from favorable (like butt or fillet) to unfavorable (like groove) because they require more preparation and skilled execution.
Finding the right quality, strength, and budget compromise will define the correct welding method for the specific project.
Different weld joints provide valuable insights into making high-quality, durable welds for various applications. You can pick from butt joints, for example, or more complex yet equally interesting groove welds.
This means that by considering how the weld metal would bond to the material, any questionable loads, and accessibility, welders can make educated decisions to create strong and long-lasting welds.
Mastering these techniques improves the quality of the work. Also, it becomes part of the welder skill, which leads to work in other industries and applications.
—A. The most common type of weld used in structural applications is the fillet weld, particularly in T-joints, lap joints, and corner joints. Fillet welds are favoured because they are strong, versatile, and relatively easy to execute, making them ideal for constructing frameworks, bridges, and other load-bearing structures.
—A. Choosing the right joint type depends on several factors, including the material thickness, load requirements, welding position, and accessibility. For example, butt joints are suitable for joining thick plates that require full penetration, while lap joints are often used for thin sheets that need easy alignment. Analyzing these factors helps determine the best joint type for your project.
—A. A groove weld fills the space between two bevelled or prepared edges, providing deep penetration and high strength. It is often used in butt, corner, and T-joints. A fillet weld, on the other hand, joins two surfaces at an angle without preparing the edges. Fillet welds are commonly used for T-joints, lap joints, and corner joints, providing sufficient strength without extensive edge preparation.
—A. Joint preparation is crucial because it ensures clean and adequately aligned surfaces necessary for achieving solid and defect-free welds. Preparation may involve cleaning, beveling, and aligning the edges to promote full penetration and fusion. Poor preparation can lead to issues like porosity, incomplete fusion, and weak welds that may fail under stress.
—A. The primary factors affecting weld quality include material cleanliness, welding technique, joint preparation, welding parameters (such as current, voltage, and speed), and operator skill level. Consistency in these factors helps minimize defects and produces reliable, high-quality welds.
—A. The flat position is the easiest for beginners because gravity helps maintain the weld pool, making it easier to control the bead and achieve good penetration. As skill levels increase, welders can progress to more challenging vertical, horizontal, and overhead positions.
—A. Not all welds are suitable for all positions. For example, some weld types, like groove welds, may be challenging in overhead positions due to gravity affecting the molten pool. Welders often adjust techniques, use different consumables, or change settings to accommodate various positions and ensure a high-quality weld.
—A. Common defects in welding joints include porosity, cracks, undercutting, incomplete fusion, slag inclusion, and excessive spatter. These defects can weaken the joint and compromise the overall strength and integrity of the weld.
—A. To improve the strength of a welded joint, ensure proper joint preparation, use the correct welding technique, select appropriate welding parameters, and choose suitable welding consumables. Maintaining adequate heat control and avoiding excessive weld reinforcement or undercutting can also enhance joint strength.
—A. Preheating is not always necessary, but it can benefit certain materials and applications, such as high-carbon steels, thick plates, and cast iron. Preheating slows the cooling rate, which minimizes residual stresses in the weld area, helping reduce the risk of cracking.
At Best Welder Reviews, Hamim Minhas has years of welding experience and expertise in evaluating welding tools and accessories. My goal is to provide clear, reliable and deep insights to help welders of all levels make informed decisions. Whether you're a beginner or an expert, my thorough reviews, buying guides, and tips ensure you find the right tool for every welding project.
Copyright © 2025 Best Welder Review. All rights reserved.