The Ultimate Guide to Fillet Welds and Full Penetration Welds for Stronger Joints
Fillet weld joins two angle surfaces together without sealing the joint completely. While in a full penetration weld the two parts are joined throughout the entire thickness hence it is a stronger connection.
Opting for a fillet weld instead of a full penetration weld is a choice that can save or wreck your project. It is easy and fast to perform a fillet weld while full penetration welds stand out as the strongest of them all. Do you wish to ensure that every joint in your structure is the best possible one? Determine what type of weld is suitable for you.
A fillet weld is ideal for quick simple connections without needing full penetration. It’s commonly used in non-critical joints. A full penetration weld on the other hand provides a much stronger bond by fully fusing the metal. This type is essential for projects needing maximum strength, like structural or pressure sensitive applications.
What is a Full Penetration Weld?
A full penetration weld is a welding technique with the weld filler completely filling up on the thickness of the joint in the metals being welded. In this case, it provides a strong hold from one side of the material to the other. It is applied in projects that demand higher strength and endurance.
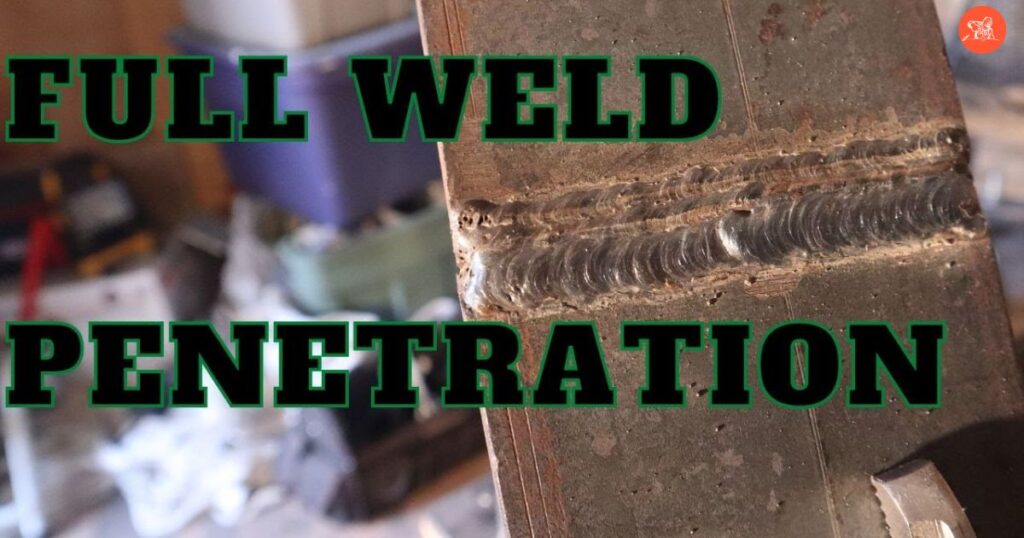
These are mostly employed in building in the forms of bridges pipes and pressure vessels. This kind is fully penetration meaning there are no loose points or weaknesses on the weld which makes it ideal for hard applications. Only a professional welder can perform this kind of weld using appropriate procedures.
What is the difference between full penetration weld and fillet weld?
A full penetration weld fuses the entire thickness of the pieces which are being welded. This enables a strong attachment across the whole junction.
A fillet weld joins two surfaces oriented at an angle without penetrating the thickness of the base metal. The processes are faster and easier to perform but are less effective in providing strength.
Welds with full penetration are seldom found in ordinary structures except in bridge works and vessels under pressure. This type of weld guarantees strength and reliability in critical applications.
Fillet welds are more common in less demanding projects. They are ideal for simple non-critical joints where full strength is not required.
Why is Full Penetration in Welding Important?
Finally, welding achievement of full penetration is very crucial since, by doing so one ensures that the joining is fully fused between one side and another. This always results in stronger and longer-lasting joints of metal parts. It is indispensable for projects requiring maximum safety and robustness.
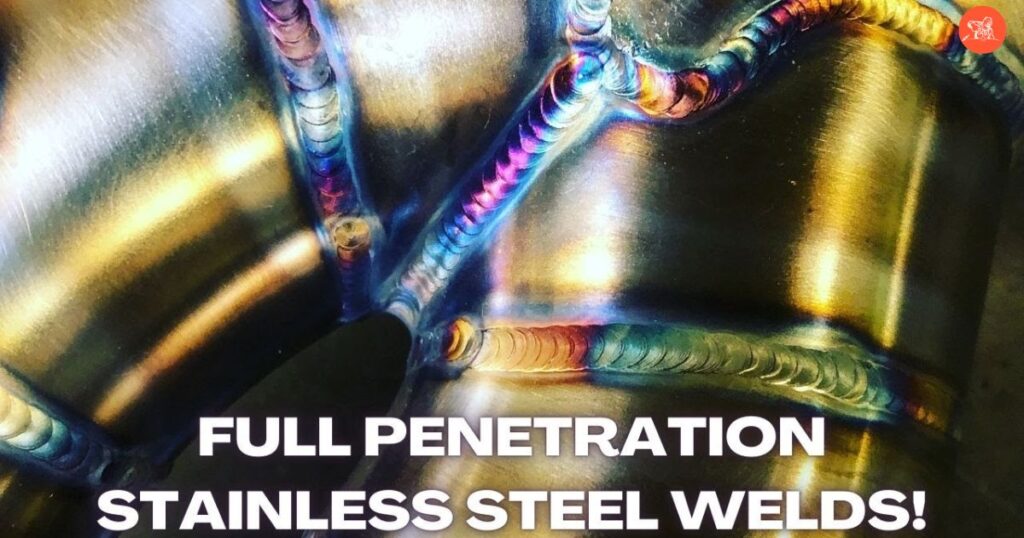
In applications like bridges pipelines and heavy structures full penetration prevents weak points that could lead to failure. It also improves resistance to stress and pressure making it the best choice for high-load environments.
High Strength – How strong is a full penetration weld?
A full penetration weld is extremely strong because it fully joins two metal pieces from top to bottom. This ensures that the entire joint can handle heavy loads and stresses. It’s much stronger than a partial penetration or fillet weld.
These welds are used in critical structures like bridges and pressure vessels where maximum strength is needed. The full fusion of metals ensures no weak points, making the weld highly reliable under extreme conditions.
Corrosion Resistance
The capacity of a specific material or weld to withstand damage from the adverse effects of water, chemicals or any other environmental aggression is known as corrosion resistance.
A full penetration weld seam is free of any gaps or voids making it impermeable to corrosion. This means that therefore, water would not able get inside the joint and hence there would be no corrosion.
Elements employed in welding processes that are not prone to corrosion are usually chosen for their strength under severe working conditions.
Improving corrosion resistance extends the life of structures especially in wet or chemical-heavy environments. It’s crucial for industries like marine, chemical plants and pipelines.
How to Achieve a Full Penetration Weld?
Achieving a full penetration weld is a process that starts with establishing the correct welding parameters. In such a case, the most effective welding current is that which ensures full thickness penetration of the weld in the work piece.
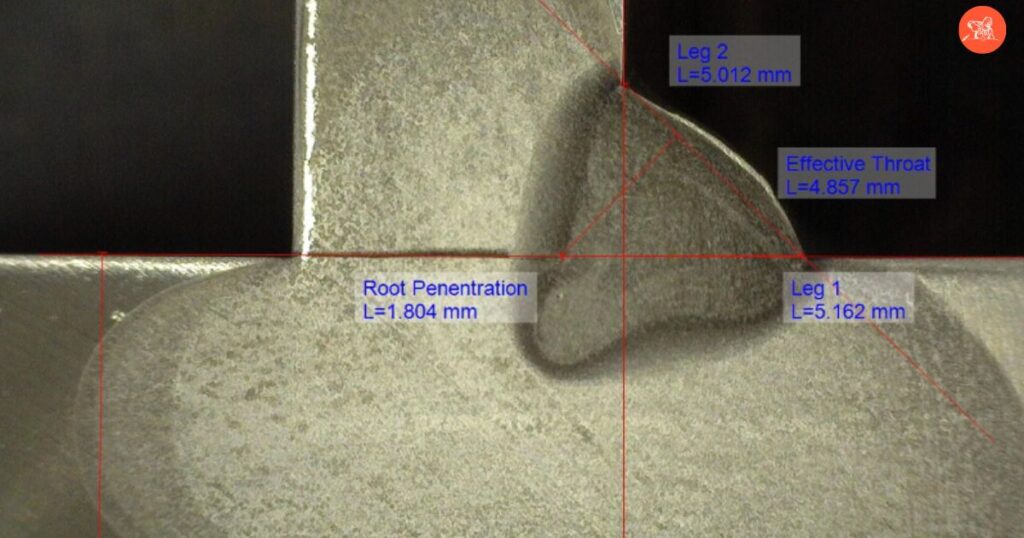
Welders must try to keep a low travel angle in balance with an even travel speed. This ensures proper heat application over the joint for better fusing. The proper choice of electrode is crucial for effective penetration and quality of the weld.
High Current
High current is crucial for achieving a full penetration weld. It provides enough heat to melt the metal completely through the joint.
When using high current the welder can create deeper welds. This ensures that the bond between the materials is strong and durable.
However, too much current can lead to overheating. This may cause burn through or distortion in thinner materials.
Welders must balance high current with other parameters. This includes voltage and travel speed to ensure a quality weld without damaging the materials.
Voltage: Not Too High or Too Low
- Sustained Arc Stability: Proper voltage is fundamental in sustaining the welding are leading to uniform heat with time.
- Right Level of Penetration: Insufficient penetration can be caused by low voltages, whereas high voltages can result in flooding of the surface melted and burn-through.
- Weld Quality: Correct voltage settings improve the weld bead profile, hence enhancing weld quality.
- Material Compatibility: Specific voltage variations are needed for various materials of different thickness for best results.
- Preventing Defects: The appropriate voltage helps minimize defects like porosity or undercutting in the final weld.
Low Travel Angle
A low travel angle is essential for achieving a full penetration weld. This angle allows the welder to direct heat more effectively into the joint. It helps ensure that the weld penetrates deeply through the thickness of the material.
Using a low travel angle also improves control during the welding process. It reduces the risk of defects such as uneven beads or incomplete fusion. Maintaining this angle contributes to a stronger and more reliable weld.
Balanced Travel Speed
Balanced travel speed is important for achieving a full penetration weld. It ensures that the welder moves at a consistent pace while maintaining adequate heat input. This helps create a strong bond between the metal pieces.
Moving too quickly can lead to insufficient penetration and weak joints. Conversely traveling too slowly may cause excessive heat, leading to burn through. A balanced travel speed is key to producing a high-quality weld.
Polarity
Polarity refers to the electrical orientation of the welding current. In welding the proper welding polarity must be used for complete penetration to be obtained. The more commonly used settings are direct current electrode positive (DCEP) and direct current electrode negative (DCEN).
DCEP is often preferred for full penetration welds. It allows more heat to be directed into the work piece promoting deeper penetration. Choosing the right polarity helps ensure a strong and reliable weld.
Electrode Selection
Electrode selection is crucial for achieving a full penetration weld. The right electrode can significantly impact the weld quality and strength.
Different electrodes are designed for specific materials and welding processes. Common types include stick, TIG and MIG electrodes each suited for different applications.
Using the correct electrode diameter is also important. A larger diameter may be needed for thicker materials to ensure adequate heat and penetration.
Welders should consider the coating type and material properties when selecting electrodes. This ensures compatibility with the base metals and optimal weld performance.
Downsides of Full Penetration Welding
Full penetration welds are not without disadvantages. It takes more time and skill than the usual versions of this method which can increase the total labor costs. Also, in this type of welding there could be additional preparation and cleaning of the surfaces to be welded.
Warping or distortion of thinner sections because of excessive heating is another disadvantage. Full penetration welds can result in defects that weaken the joint if they are completed incorrectly. Because of these reasons full penetration welding is not ideal for certain assignments.
FAQ’S
Q1. What is a fillet weld?
—A. A fillet weld connects two surfaces at a right angle.
Q2. What is a full penetration weld?
—A. A full penetration weld completely melts through the thickness of the materials.
Q3. When is a fillet weld used?
—A. Fillet welds are used for simple joints where full strength isn’t required.
Q4. Why is full penetration welding important?
—A. Full penetration welding guarantees a more sturdy and robust connection in crucial applications.
Q5. Can you convert a fillet weld to a full penetration weld?
—A. Yes, you can adjust techniques and settings to achieve full penetration.
Conclusion
In order to perfect element projects, it is important to appreciate the distinction in the use of a fillet weld and full penetration weld. Strain fillet welds are however unsound as they are easy and quick in closing the gaps which makes they unfit for important work.
It is essential to select the appropriate weld based on the requirements of the project at hand. For example, bridges and pipes where safety interest is paramount, require full penetration welding which guarantees a strong joint. Full penetration welding is the most popular way to ensure maximum effectiveness of the welder’s works on their tasks.
Also Read Must About Welding: