Suitable Welding VS Bad Welding - What Makes the Difference
In construction and manufacturing, welding quality is critical. Knowing the difference between excellent and lousy welding is vital. It ensures metal projects are safe and last long. Poor welding can cause failures, leading to high costs and safety risks.
This article will show you the difference between quality and substandard welding. We’ll use examples and give tips. We aim to improve your welding skills, ensuring each weld is up to standard. This will help keep your projects safe and durable.
Key Takeaways
- For larger metal projects, the welding quality is directly proportional to the usability or safety of these works.
- One of the leading causes of failure in any project and cost escalation is poor welding practices.
- Good welding techniques are the base of good welds.
- Welding Work Can Be Done Reliably Only by Using Good Quality Materials
- Good practices and mistakes in welding can be mastered only if proper training is provided.
Understanding Good Welding Practices
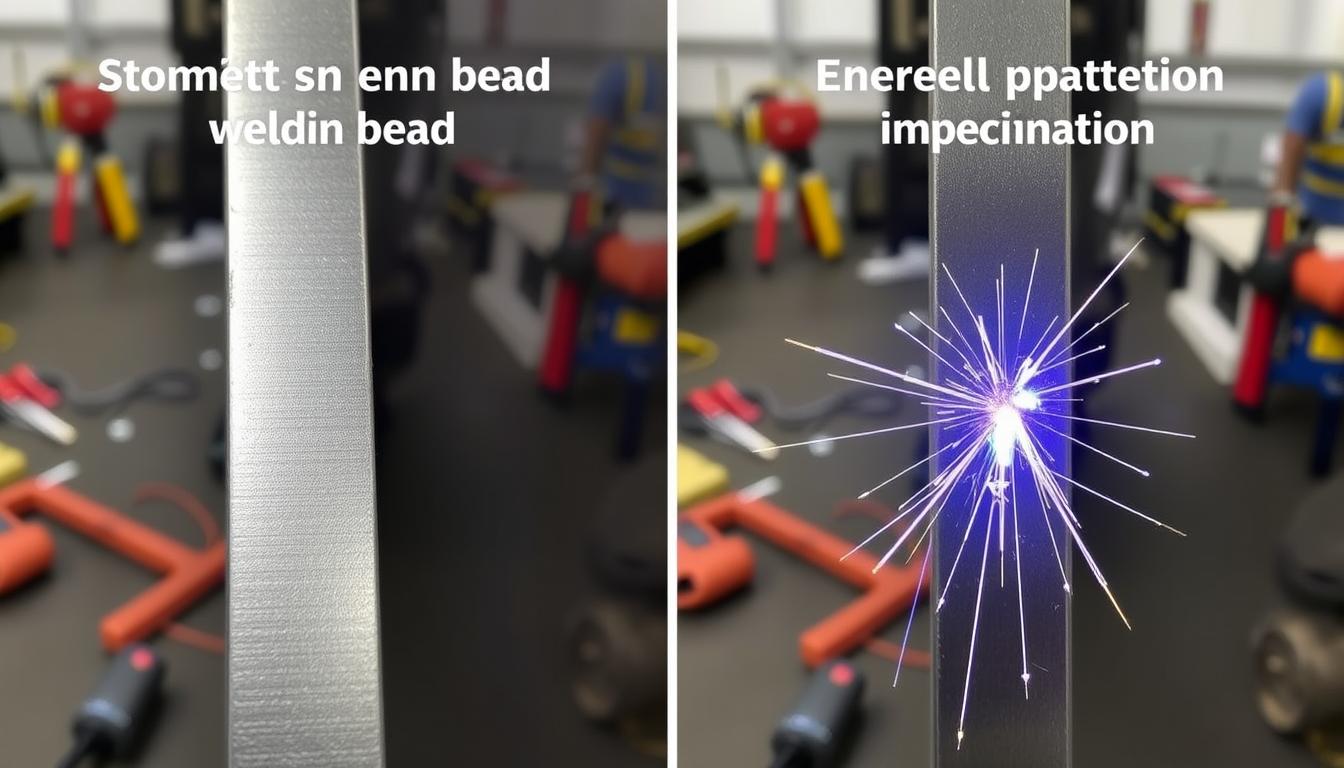
Suitable welding involves many essential factors that help achieve the best results in metalwork. Knowing these- factors means- understanding welding techniques, skilled practices, and- ongoing education.
Critical Techniques for Quality Welding
Quality weldings starts with mastering vital techniques. These include:
Electrode Handling:
- Maintaining temperature to avoid warping from excessive melting.
- Amperage Control: Changing the current based on the thickness and type of material
- Welding is one of those areas evaluated in an examination of efficient welding techniques. Both of these greatly influence the strength and visual appeal of the weld.
Importance of Proper Training
Effective education and practice create skilled welders. AWS offers certifications through- its various programs, guaranteeing that the welders possess- the required talent. Metalwork must be more of continuing education and practice to maintain high standards.
Use of High-Quality Materials
Choosing top-tier materials is crucial. The suitable filler metals, shielding gases, and base materials make a strong weld. Here’s a table showing how material quality affects welding results.
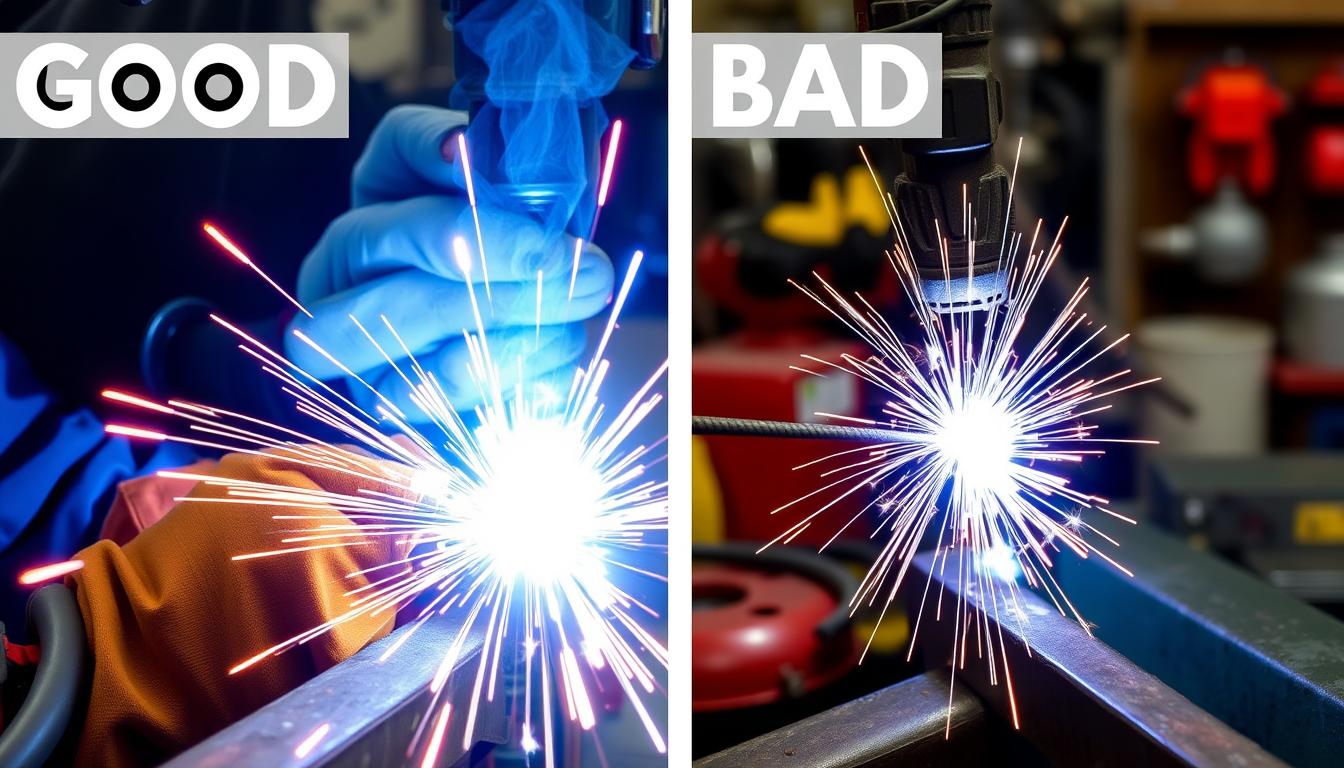
Aspect | High-Quality Materials | Low-Quality Materials |
Durability | Highly Durable | Less Durable |
Consistency | Consistent Performance | Inconsistent Performance |
Endurance | Longer Endurance under Stress | Prone to Fail under Stress |
Appearance | Smooth and Clean | Rough and Irregular |
Common Welding Mistakes to Avoid
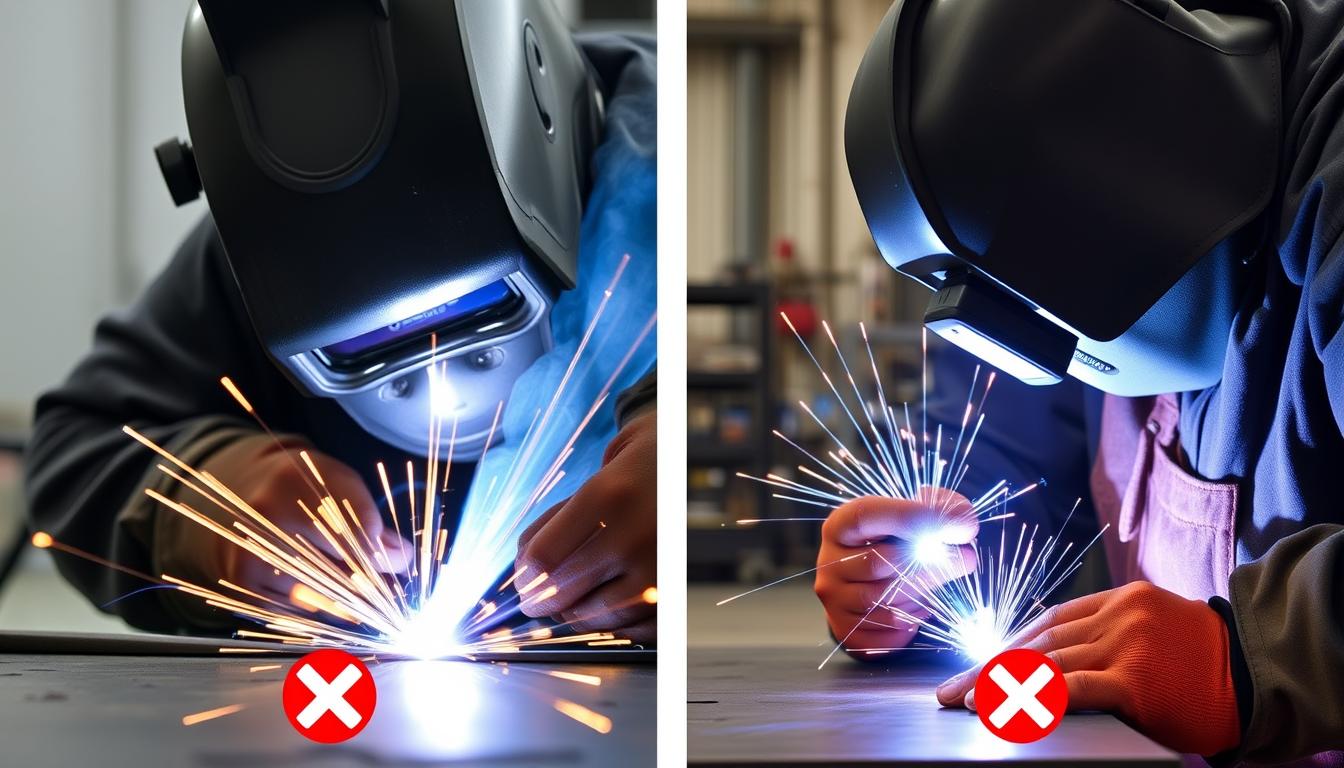
Knowing common mistakes is vital when aiming for top-notch welding. Let’s explore some common errors and how to avoid them.
Incorrect Heat Settings
One big mistake is using the wrong heat settings. Getting the heat right is vital for strong, clean welds. Too much heat can cause weak spots, while too little leads to spatter.
Adjusting your welding machine to the suitable material and thickness is crucial.
Inadequate Surface Preparation
Another mistake is not preparing the welding surface well enough. A clean, free surface is essential for a good weld. With proper prep, you might get stronger welds and more defects.
Poor Joint Alignment
Another big mistake is incorrect joint alignment. Joint alignment is essential for the weld’s strength and stability. If joints are off, stress won’t be evenly spread, leading to weld failure.
We can dodge these mistakes by focusing on heat management, surface prep, and joint alignment. This way, we get better welding results.
Welding Quality Comparison: Good vs Bad Welding
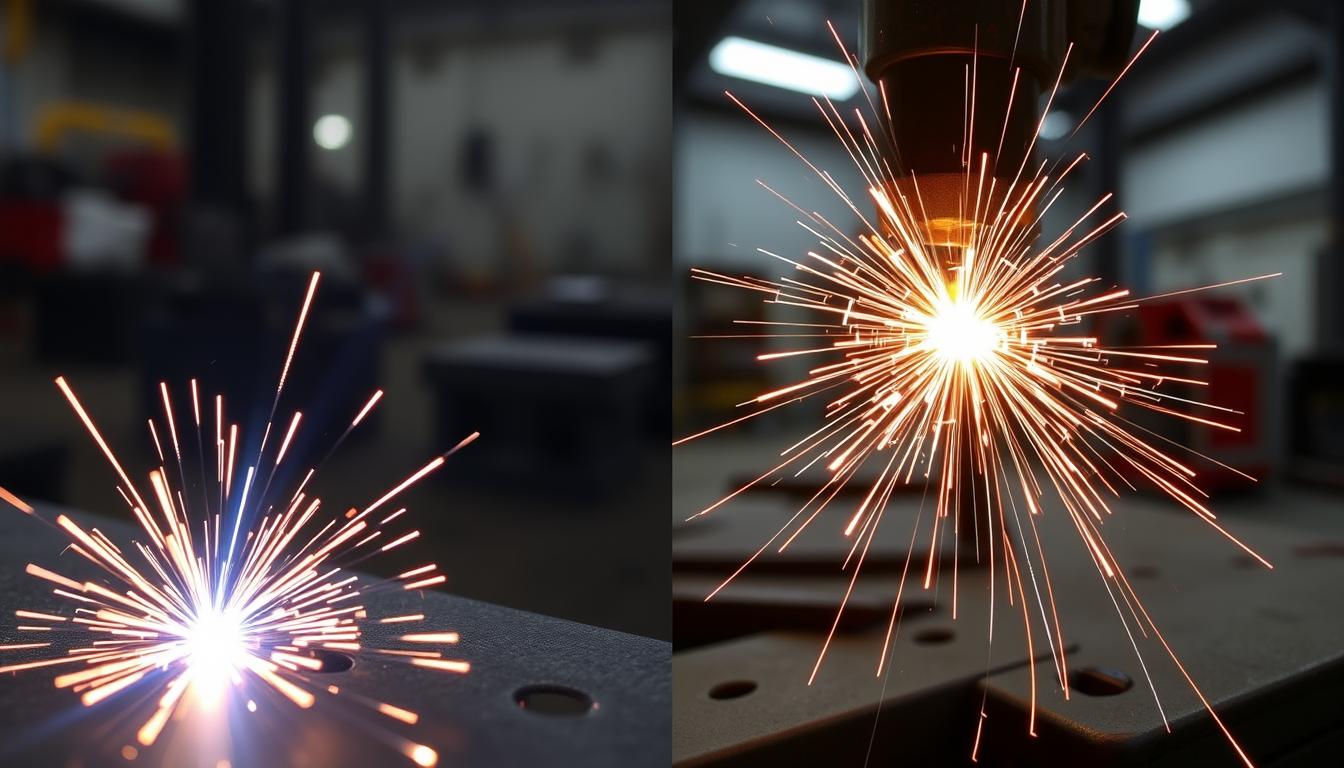
Knowing the difference between excellent and lousy welding is critical to ensuring safety and quality in any project. Welding quality inspection helps by following industry standards.
Suitable welding produces clean, strong, and even welds that meet or exceed industry standards. They also have consistent beads, proper Penetration, and little splatter.
On the other hand, lousy welding results in uneven beads, poor Penetration, and many defects, such as cracks or porosity.
Aspect | Good Welding | Bad Welding |
Appearance | Smooth, even beads | Ragged, inconsistent beads |
Penetration | Proper full penetration | Inadequate or excessive penetration |
Defects | Minimal to none | Cracks, porosity, and inclusions |
We can spot and fix problems early by using strict welding quality inspection. This keeps welds safe and durable. It also helps us distinguish suitable welding from bad.
Top Welding Practices for Optimal Results
Using the best welding practices leads to high-quality welds, making the welding area safer and more efficient.
Maintaining a Clean Workspace.
A clean workspace- significantly affects weld quality. Keeping it tidy reduces fire- risks and makes- tools easy to find. This follows the rules of a well-organized welding area.
Regular Inspection and Maintenance of Equipment
Checking and fixing welding tools regularly is critical. It prevents failures during essential tasks. A regular maintenance- plan keeps equipment working well, ensuring consistent welds.
Identifying Welding Defects and Their Prevention
Finding and fixing problems- during welding is critical to a top-notch finish and durable results. Knowing common welding defects and prevention methods can significantly improve the accuracy of our work.
Common Types of Welding Defects
Many welding defects can happen if we don’t follow the proper steps. The most common ones are:
- Porosity: Gas bubbles in the weld metal can weaken the joint. This is often due to dirty materials or harmful gas shielding.
- Cracks: These are breaks in the weld area. They can be caused by too much stress, lousy welding methods, or fast weld cooling.
- Incomplete Penetration occurs when the weld doesn’t fully join the parts. It’s usually caused by needing- heat or using the wrong technique.
Techniques to Prevent Defects
It’s crucial to use prevention methods to avoid welding flaws. Here are some key ways for welding defects prevention:
- Quality Welding Inspection: Regular checks during and after welding can spot problems early, making- fixing them easier before they become significant issues.
- Proper Material Selection: Using top-quality materials and adequate storage and handling can lower contamination risks and help prevent defects like porosity.
- Appropriate Heat Settings: The proper heat settings for the materials and welding methods ensure full Penetration. This helps avoid cracks.
Combining strict quality welding inspection with following best practices leads to welding defect prevention and suitable welding flaw identification.
Expert Welding Tips for Enhanced Quality
To get top-notch welds, you need the right mix of skill, precision, and always getting better. Here are our top tips to boost your welding game. They cover advanced techniques, how to check your work after welding, and ways to keep improving.
Choosing the Right Welding Technique
Picking the correct welding method is critical for great results. Knowing your material and project is essential whether you’re using MIG, TIG, or Stick welding. MIG is best for thick materials and fast projects. TIG is perfect for thin materials or detailed work. Stick welding works well outdoors because it handles harsh conditions well.
Post-Welding Inspection Procedures
It’s vital to check your welds carefully after welding. Look for cracks, porosity, or undercuts. Use your eyes and tools- like ultrasonic or radio graphic testing to find hidden- flaws. This ensures your welds are safe and last long.
Continuous Learning and Improvement
The welding world is constantly changing with new methods and tools. Joining professional development programs and using resources from groups like the American Welding Society keeps you updated. Learning new things expands your skills and gives you the latest project tips.
Technique | Use Case | Advantages |
MIG Welding | Thicker Materials | Speed and Efficiency |
TIG Welding | Thinner Materials | Precision and Control |
Stick Welding | Outdoor Applications | Durability and Adaptability |
Conclusion
This is especially important for anyone working with excellent or lousy welding. It involves welding—the right methods, well-trained personnel, and high-quality material. These steps are essential to building strong and lasting products.
It helps avoid mistakes, poor heat settings, and surface preps. Pues ahora que ya desist por la tecnisida de person all the unnecessary junkie ness of a poorly aligned joint; Such mistakes do not only pose a threat to safety but also degrade the quality of work. By concentrating on such areas, we can enhance our welding capabilities and also ensure better output.
Success largely depends on adhering to top welding practices. These include keeping the place clean, taking care of your stuff, and welding at a constant rate.
Freequently Asked question about Good Welding VS Bad Welding
Q1. What are the main differences between suitable welding and bad welding?
—A. Suitable welding makes things last longer and is safer. It meets high standards and passes tests. Bad welding can be weak, risky, and expensive. It depends on the welder’s skill and the quality of the materials.
Q2. What essential techniques contribute to quality welding?
—A. Quality welding needs heat, clean metal surfaces, and correct joint alignment. Training welders and using the right tools are also crucial. This ensures solid and lasting welds.
Q3. Why is proper training necessary for welders?
—A. Training helps welders do their jobs well. They learn safety rules and how to fix problems, which makes them better and more reliable.
Q4. How do high-quality materials impact welding quality?
—A. Suitable materials mean fewer problems in the weld. They also stick better and last longer, making the weld stronger and safer.
Q5. What are common welding mistakes to avoid?
—A. Mistakes include wrong heat, improper metal cleaning, and bad joint alignment. These can cause weak welds and failures. Paying attention to detail helps avoid these mistakes.
Q6. How can incorrect heat settings affect welding?
—A. Wrong heat can cause the metal to not stick or get too hot, leading to weak welds and defects. Getting the heat right is crucial for a strong weld.
Q7. Why is surface preparation crucial in welding?
—A. Cleaning the metal surface is critical for a strong bond. Poor preparation can cause weak welds and defects. Clean surfaces are essential for suitable welding.
Q8. How does joint alignment influence welding quality?
—A. Proper alignment strengthens and protects the weld, while bad alignment can weaken it. It’s essential for the weld’s integrity.
Q9. What factors should be considered during welding quality inspection?
—A. Inspect weld size shape and for defects. Check if it meets standards and is structurally sound. Following industry guidelines is essential for a thorough check.
Q10. What are- the benefits- of maintaining a clean- workspace when welding?
—A. A clean workspace prevents contamination and ensures equipment works right. It keeps things safe and helps make high-quality welds.
Q11. How does regular inspection and maintenance of welding equipment affect results?
—A. Regular checks and upkeep keep equipment working well, reducing defects and failures. Well-maintained equipment leads to better welds.
Q12. Why is consistent welding speed critical?
—A. Consistent speed ensures even heat and a good weld. Wrong speed can cause defects. It’s essential for a strong and good-looking weld.
Q13. What are common types of welding defects?
—A. Defects include porosity, cracks, and weak welds. These weaken the weld and can be dangerous, reducing its strength and safety.
Q14. What techniques help prevent welding defects?
—A. Use the proper heat, prepare joints well, and keep surfaces clean. Follow welding rules and practice often to avoid defects.