Top-Rated Underwater Welding Solutions
Typical depth of underwater sea lines welding: In the offshore oil and gas world, underwater welding is key. It keeps the infrastructure strong, fixes damage, and builds new projects. This guide looks at the depths and methods used in underwater welding. It also discusses the challenges and how to solve them in this special field.
Subsea welding is crucial for fixing and building offshore pipelines and platforms. Knowing the proper welding methods for each depth is essential. This guide covers the basics of underwater welding, discussing the main things to consider and the best ways to do it.
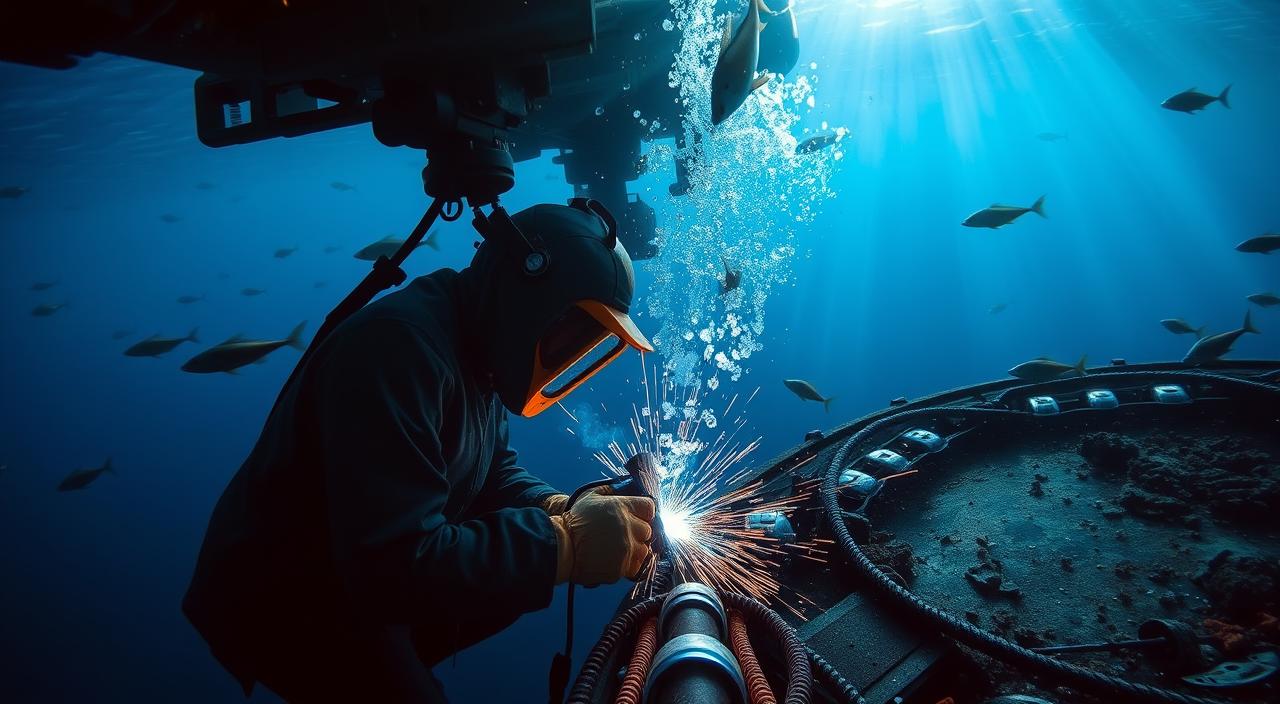
Key Takeaways
- Explore the typical depth ranges for underwater sea lines welding operations
- Understand the differences between wet welding and dry hyperbaric welding methods
- Gain insights into the environmental factors that impact welding quality in subsea environments
- Discover the essential equipment and technology required for deep-sea pipeline welding
- Learn about the certification requirements and professional training for subsea welding personnel
- Explore safety protocols and risk management strategies in subsea welding operations
- Understand the importance of emergency response procedures and decompression management.
Understanding Underwater Welding Fundamentals and Depth Classifications
Underwater welding is a particular job that needs a lot of knowledge. It’s done in water, where things are different. Wet and dry hyperbaric welding are two main ways to weld underwater.
Wet welding is done in the water. The welder wears a special suit and helmet. It’s simple and cheap but can only go so deep.
Dry hyperbaric welding is done in a pressurized chamber, which allows the welder to work in a dry place. It’s more expensive but can go deeper.
Wet Welding vs. Dry Hyperbaric Welding Methods
Wet welding happens in the water. The welder wears a special suit and helmet. It’s simple and cheap but has depth limits.
Dry hyperbaric welding uses a pressurized chamber. It lets the welder work in a dry place. It’s more expensive but can go deeper.
Maximum Operational Depth Limits
Wet welding can go up to 300 feet deep. Dry hyperbaric welding can go up to 1,000 feet deep or more. Going deeper can be risky.
Environmental Impact on Welding Quality
The underwater world affects welding quality a lot. Things like water currents and temperature matter. Special training and equipment are needed for good welds underwater.
Welding Method | Maximum Operational Depth | Environmental Factors Affecting Welding Quality |
---|---|---|
Wet Welding | 300 feet (90 meters) | Water currents, temperature, contaminants |
Dry Hyperbaric Welding | 1,000 feet (300 meters) or more | Increased pressure, reduced oxygen levels |
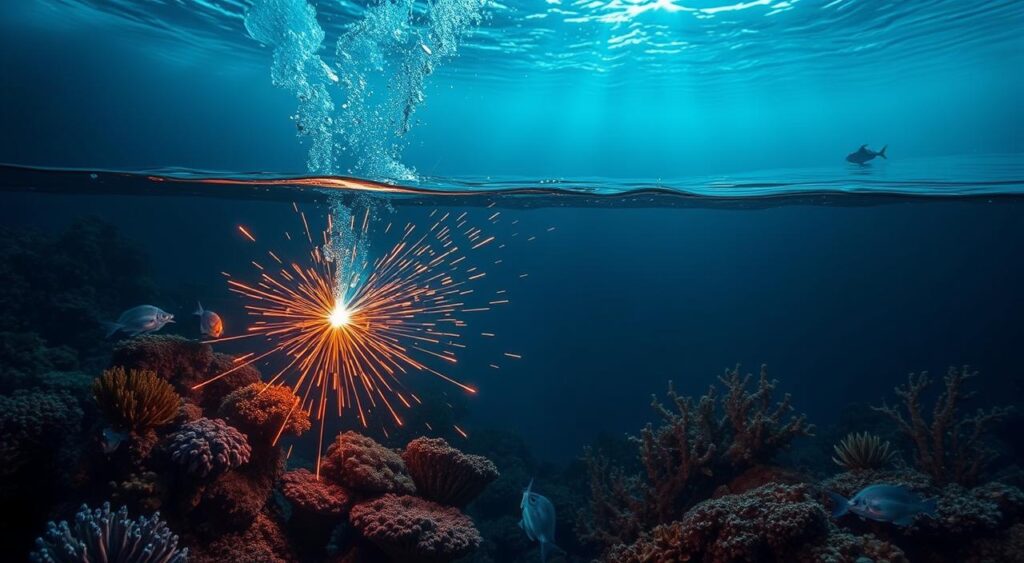
Typical Depth of Underwater Sea Lines Welding: Standards and Specifications
Offshore pipeline welding is very important. The depth of the seabed affects the welding methods and tools needed. There are standards and specs to make sure underwater welding is done safely and well.
Underwater sea lines welding is divided into three main depth ranges:
- Shallow Water Welding: Done up to 50 meters deep. It uses wet welding and subsea welding equipment for shallow water.
- Intermediate Water Welding: Done between 50 and 200 meters deep. It needs dry hyperbaric welding and underwater welding habitat systems.
- Deep-Water Welding: Done over 200 meters deep. It requires advanced offshore pipeline welding procedures and subsea welding equipment for high pressure and tough conditions.
Each depth range has its own challenges. It needs special welding methods, tools, and safety rules. Following industry standards is key for successful offshore pipeline projects at different depths.
Depth Range | Welding Technique | Equipment Requirements |
---|---|---|
Shallow Water (up to 50m) | Wet Welding | Subsea welding equipment, waterproof electrodes |
Intermediate Water (50-200m) | Dry Hyperbaric Welding | Underwater welding habitat, specialized power sources |
Deep Water (above 200m) | Highly Advanced Offshore Pipeline Welding | Robust subsea welding equipment, remote-controlled systems |
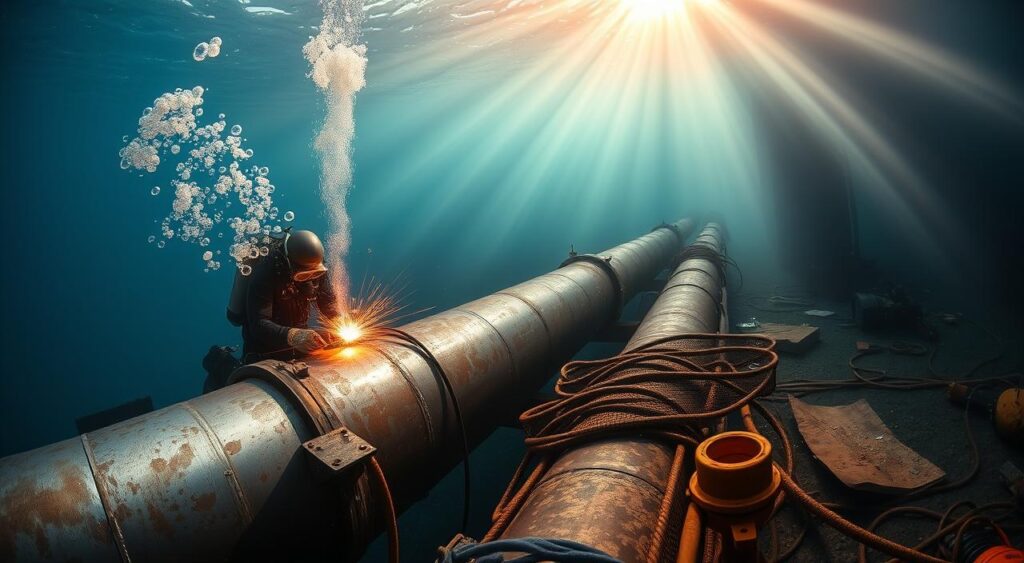
Essential Equipment and Technology for Deep Sea Pipeline Welding
Deep sea welding is tricky. It needs special tools and new tech. Things like advanced welding machines and special underwater electrodes help a lot.
Advanced Welding Power Sources
Welding under the sea is challenging because of the deep water. New welding machines are made to handle this. They work better and are more precise.
These machines can handle the pressure and harsh sea conditions. They make sure welding works well, even in the most challenging places.
Specialized Underwater Electrodes
Welding underwater needs special electrodes. They must resist the sea’s pressure and keep working well. The electrodes have special coatings and formulas.
This makes them strong and helps them weld well, even deep down. New designs also improve and strengthen the welds.
Safety and Monitoring Systems
Welding deep underwater is risky. That’s why safety systems are critical. They watch the air, help in emergencies, and use robots for welding.
These systems help keep- everyone safe and ensure that work goes smoothly. They’re essential for deep-sea welding.
Thanks to new tools and technology, deep-sea welding is improving. Workers can do their jobs safely and competently, which suits everyone involved.
Equipment/Technology | Key Features | Benefits |
---|---|---|
Advanced Welding Power Sources | Inverter-based design Enhanced efficiency and control Pressure and environment-resistant | Reliable performance in deepwater conditions Precise control over welding parameters Improved energy efficiency |
Specialized Underwater Electrodes | Corrosion-resistant coatings Engineered flux formulas Enhanced arc stability and weld quality | Maintain integrity in high-pressure environments Consistent, high-quality welds Reduced porosity and improved mechanical properties |
Safety and Monitoring Systems | Atmospheric monitoring equipment Emergency life support systems Remote-controlled robotic welding platforms | Mitigate risks in deepwater welding operations Enhance operational efficiency and safety Safeguard the entire subsea welding process |
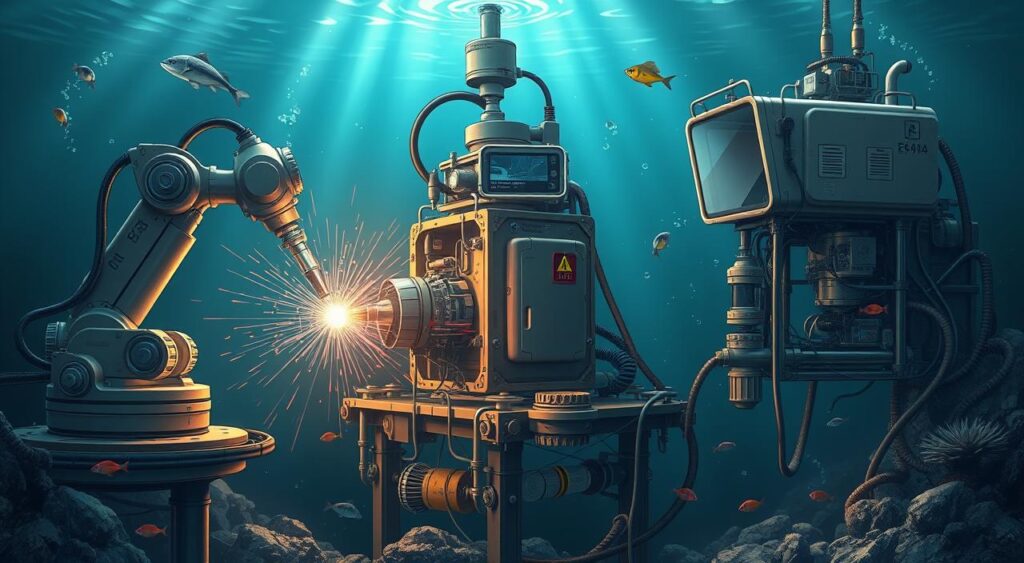
Certification Requirements and Professional Training
You must pass a strict test and get unique training to be an excellent underwater welder. You must know a lot about the challenges and safety rules of underwater welding.
The first step is getting a deep-sea welding certification. This includes extensive learning and hands-on tests, ensuring that welders can handle underwater welding well.
- Comprehensive training in underwater welding techniques, including wet welding and dry hyperbaric welding
- Mastery of specialized equipment and technology used in deep sea welding, such as advanced welding power sources and underwater electrodes
- Thorough understanding of the environmental factors that can impact welding quality, including depth classification and pressure considerations
- Proficiency in adhering to industry standards and specifications for offshore pipeline welding procedures
After getting certified, you need to keep learning. Underwater welders must know the newest tech, safety rules, and best practices. This helps them keep up with the deep sea welding world.
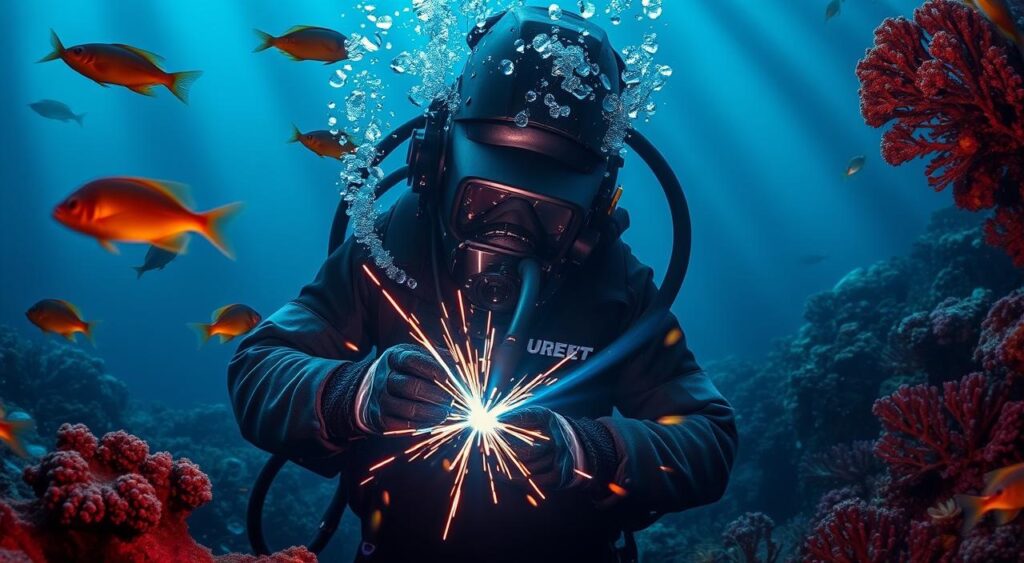
For those wanting to work on offshore pipelines or on big underwater projects, learning never stops. By working hard and staying updated, underwater welders become key players in the deep sea welding field.
Safety Protocols and Risk Management in Subsea Welding Operations
Keeping welders safe is very important in deepwater welding. This work is done in very tough underwater places. Here, the risk of things going wrong is higher.
To deal with these risks, the industry has made many safety rules. They also have plans to manage risks.
Emergency Response Procedures
Underwater welding teams need to be ready for emergencies. They have plans for quick evacuations and medical help. They also do drills to practice these plans.
Decompression Management
Welders face a big risk of getting “the bends” when they go up too fast. They use special chambers to avoid this. They also watch their depth and time underwater closely.
Communication Systems
Good communication is crucial for safe underwater welding. They use special systems for talking underwater. This helps them stay in touch and respond quickly to problems.
With strict safety rules, careful risk management, and new tech for talking, the industry keeps workers safe. They can do important work in very hard places. This is key for deepwater welding safety protocols, protecting the underwater welding habitat, and working safely at hyperbaric welding depth.
Conclusion
Underwater sea line welding is critical. This guide has covered the basics and how to do it safely. It’s about working deep in the sea.
It’s critical to know the difference between wet and dry welding. I also learned how to deal with the sea and got certified. Training, special tools, and careful planning are needed.
The industry must keep improving as more underwater work is needed. This will help our energy and transport systems stay connected.
Welding deep underwater is a big challenge, but experts are making it possible. With new tech, we can do even more underwater work.
Freequently asked question about typical depth of underwater sea lines welding
Q1. What are the typical depth ranges for underwater sea line welding?
—A. Underwater sea line welding can be done at different depths. It depends on the project and location. Here are the typical ranges:
- Shallow water: Up to 50 meters (164 feet)
- Intermediate depth: 50 to 200 meters (164 to 656 feet)
- Deep water: 200 to 1,000 meters (656 to 3,281 feet)
- Ultra-deep water: Beyond 1,000 meters (3,281 feet)
Q2. What are the critical differences between wet Welding and dry hyperbaric welding methods?
—A. There are two main underwater welding methods. They are wet Welding and dry hyperbaric Welding:
- Wet Welding: Done in the water, it’s for shallower depths up to 50 meters. It needs special waterproof gear and electrodes. It’s more affected by water conditions.
- Dry Hyperbaric Welding: This welding technique is done in a pressurized, dry space. It is used for more profound depths and produces better welds. A unique underwater chamber is needed for dry conditions.
Q3. What are the maximum operational depth limits for different underwater welding techniques?
—A. The depth limits for underwater Welding depend on the method:
- Wet Welding is usually up to 50 meters (164 feet) deep, and it’s difficult to do it deeper because of the water.
- Dry Hyperbaric Welding can go up to 1,000 meters (3,281 feet) or more. It requires special gear and steps to keep it dry.
Q4. How do environmental factors impact the quality of underwater Welding?
—A. Water temperature, currents, visibility, and pressure affect underwater Welding. They can change the weld quality. Planning well, using the right gear, and having skilled people are essential.
Q5. What are the industry standards and specifications for underwater sea line welding at different depths?
—A. There are standards for underwater Welding based on depth:
- Shallow Water: AWS D3.6M covers wet Welding here.
- Intermediate and Deep Water: API and ISO have stricter rules for deeper water.
- Ultra-Deep Water: Advanced hyperbaric Welding and special gear are needed for extreme depths.
Q6. What types of specialized equipment are used for deep-sea pipeline welding?
—A. Deep-sea Welding needs special gear, like:
- Advanced Welding Power Sources: They keep the arc stable in deep water.
- Specialized Underwater Electrodes: They help make strong welds in deep water.
- Subsea Welding Habitats and Chambers: They create a dry space for welding deep.
- Sophisticated Safety and Monitoring Systems: They keep welders safe and watch the welds.
Q7. What are the certification requirements and training programs for underwater welders?
—A. Underwater Welding needs a lot of training and certification:
- Certifications: Welders get certified by AWS or IMCA. It shows they know Underwater Welding.
- Training Programs: Courses teach about hyperbaric chambers, Welding, safety, and emergencies. They give both theory and practice.
Q8. What are subsea welding operations’ key safety protocols and risk management strategies?
—A. Keeping underwater welders safe is very important. Some key steps include:
- Emergency Response Procedures: Plans and gear for emergencies, like rescues or equipment failures.
- Decompression Management: Rules for safe decompression to avoid “the bends.”
- Advanced Communication Systems: Good ways to talk to welders and support during underwater work.