Gmaw Aluminum Welding
What is Gmaw Aluminum Welding: GMAW (gas metal arc welding) aluminum welding is among the Aluminum joining processes that use continuous wire and shielding gas. This is comparatively quicker and gives moderately cleaner welds but strong enough for industrial purposes.
Want to get your Aluminum welded really speedily and effectively? GMAW aluminum welding is the answer for robust, apparent welds. This is the best process to combine speed with high quality and for industrial requirements. Learn why it’s desired in aerospace automotive applications and much more.
As this welding is commonly used in the wire feed, it is generally known as MIG for shielding gas aluminum weld. Primarily old in the automotive and aerospace industries. That’s one reason they make it work; it’s fast. Being set up right is also critical.
Welding Power Supplies and Materials
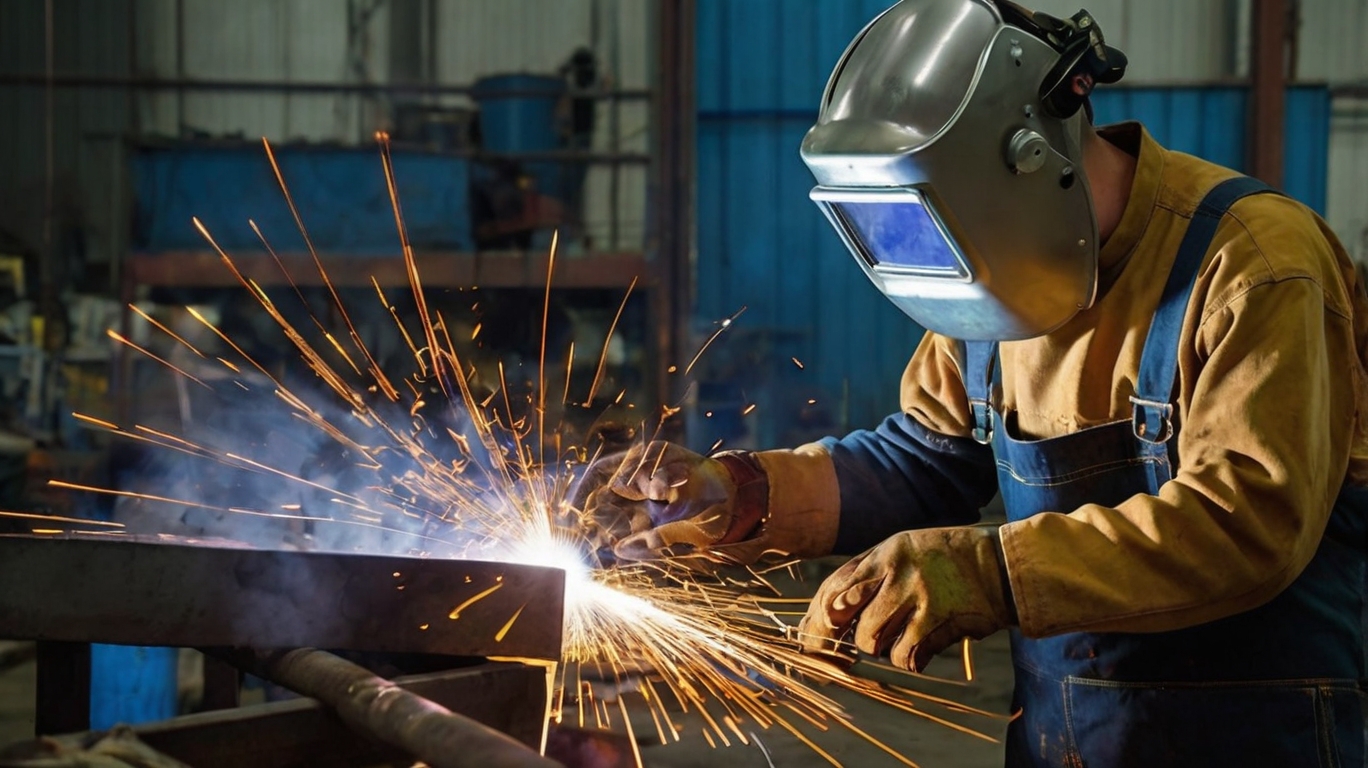
What is Gmaw Aluminum Welding
GMAW aluminum welding requires a reliable power supply for consistent results. A constant-voltage power source is best for keeping the arc stable. This setup allows welders to adjust settings precisely for Aluminum.
Using suitable materials is also essential for quality. Aluminum filler wires like ER4043 or ER5356 are commonly used for strength and compatibility. Argon gas is the preferred shielding gas to protect the weld from impurities.
Gmaw Aluminum Welding Parameters
GMAW aluminum welding requires specific parameters for a stable, strong weld. Voltage and amperage must be adjusted carefully to maintain a steady arc. Wire feed speed also crashes how much filler is added to the weld.
Direct Current Power Supply
A direct current (DC) power supply provides a constant voltage for welding. It helps create a stable arc, which is essential for high-quality welds.
Welding Wire
Welding wire is the filler material used in GMAW aluminum welding, where it melts into the bond of two pieces of Aluminum.
Shielding Gas
Shielding gas keeps the weld area safe from contamination in GMAW aluminum welding. Argon is the most commonly used gas in this context.
Advantages and Disadvantages of GMAW Aluminum Welding
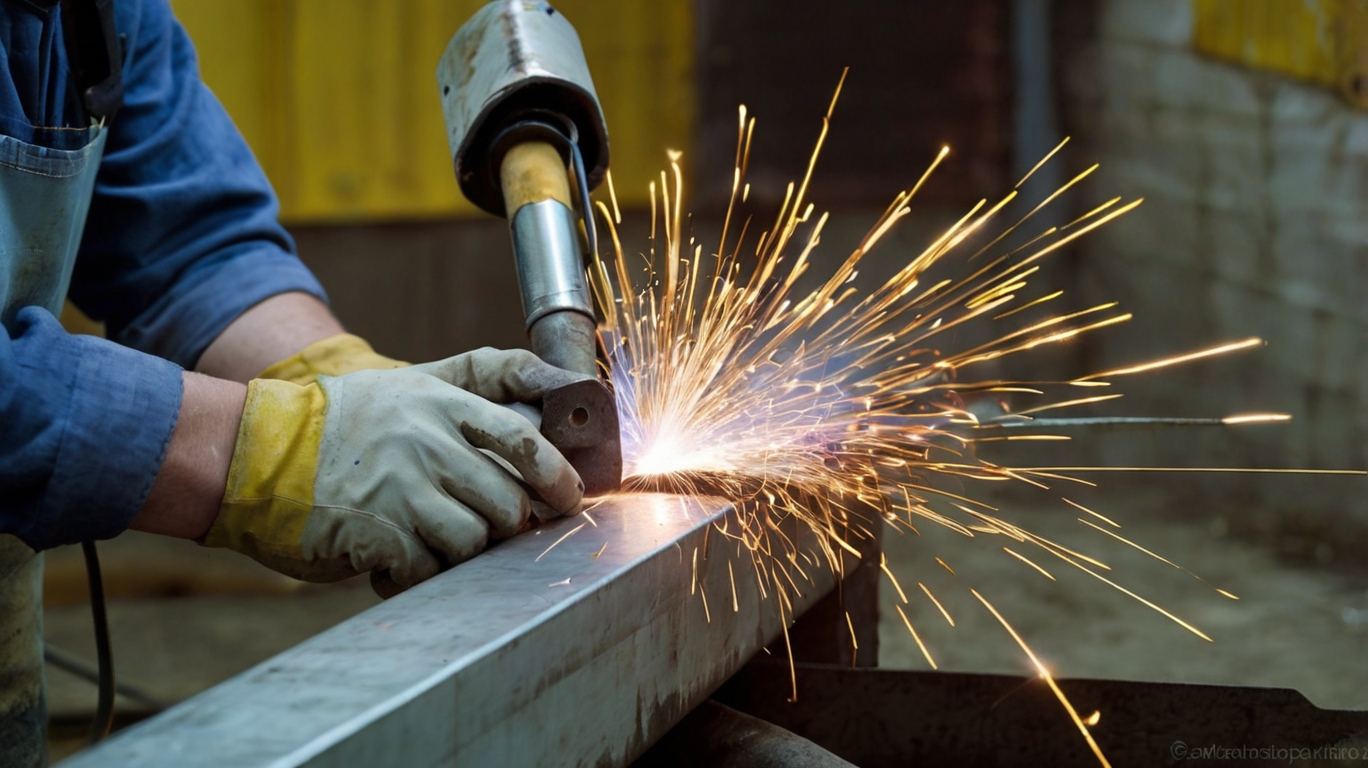
The GMAW aluminum welders can be clean and tough enough to make high-output work fast and sturdy for industrial applications. They are also versatile since they get thicker with the proper setup.
Due to the high heat input, GMAW aluminum welding could be impractical if the material is thin. Surface cleanliness is crucial, as dirt or oxidation severely jeopardizes the weld. It requires more control, so it is less flexible with inexperienced welders.
Application of GMAW Aluminum Welding
What is Gmaw Aluminum Welding
GMAW welding of Aluminum can be commonly found in the automobile industry. It Enables Lightweight Vehicle Bodies And Parts This process makes the car lightweight, creating an efficient vehicle.
GMAW aluminum welding that builds aerospace aircraft structures. Thus, these provide well-established connections and high resilience to crushing. So, this will make complex design super easy.
Shipbuilding utilizes aluminum welding, which falls under the GMAW classification. This type of welding is used to weld the hulls and other parts of boats and ships, obtaining lightweight corrosion-lingering merchandise.
Construction: GMAW aluminum welding As it supports aluminum frames or scaffolding in buildings, it is solid and lightweight, ideal for modern architecture.
GMAW Aluminum Welding Tips and Tricks
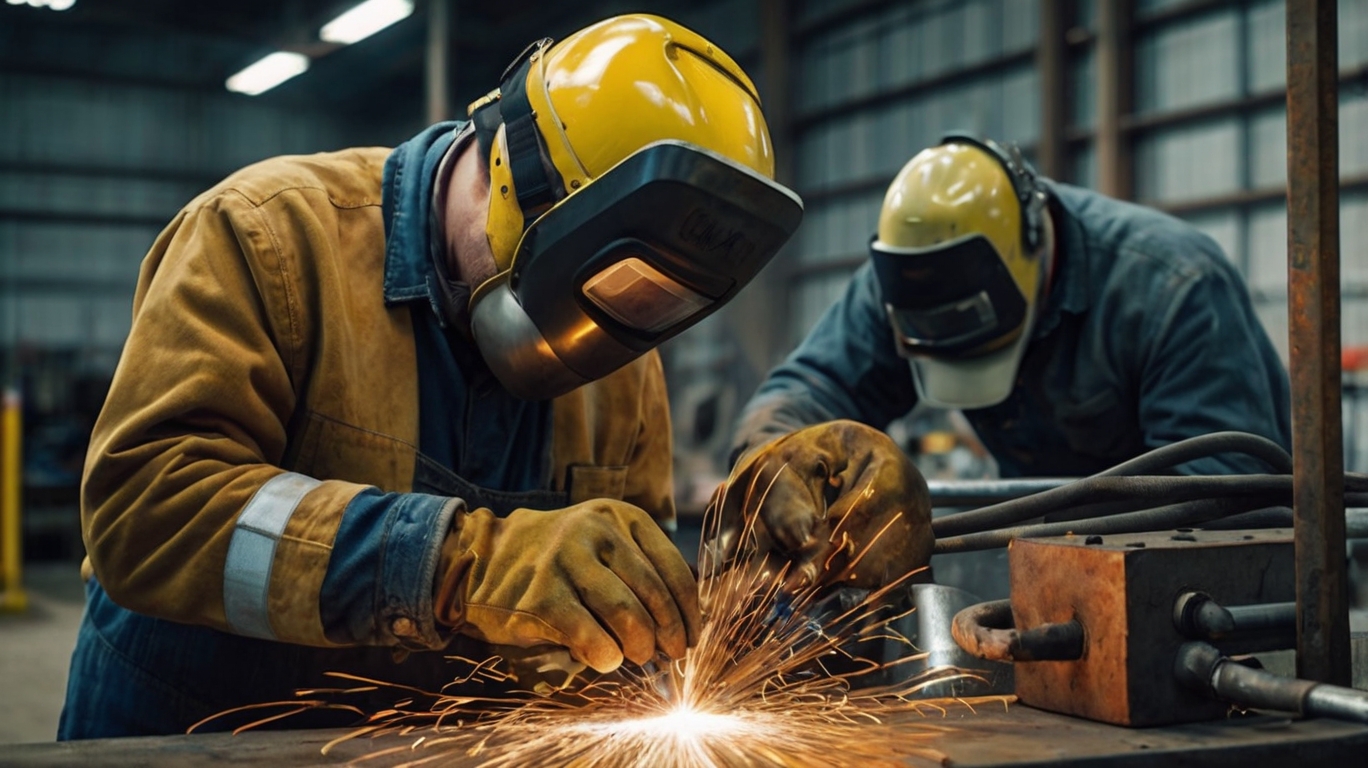
GMAW welding of Aluminum is among the fastest methods of completing a welding booth task. It is relatively fuss-free and does it fast. However, proper settings and techniques would definitely assist with achieving solid and clean welds:
- Apply appropriate filler material using a filler material near the apparent aluminum alloy.
- Surface Cleaning: Clean the metal by removing dirt and oxidation.
- Change in welding parameters. To weld well, it is essential to have the voltage and wire speed correctly set.
- Weld Aluminum with Proper Electrode: Choose the appropriate tungsten electrode for aluminum welding.
- Control the introduction of heat to prevent warping and thus ensure a good weld.
Material Selection and Matching
Successful GMAW of Aluminum is highly dependent upon their selection and matching. Answer: The filler wire must be compatible with the alloy of Aluminum to be welded. This way, the weld was going to be relatively close both in terms of strength and properties to the base material.
This ensures that materials are compatible so that there is no cracking or poor bonding. Hence, the alloys and their particular properties need to be known. Well-matched → stronger, more challenging welds that will meet an industry standard
Pre weld Preparation
GMAW aluminum welding requires many conditions to obtain quality welds; however, pre-weld cleaning is crucial. First and foremost, the aluminum surface should be free of dirt, grime, grease, and oxidation.
The surface may be contaminated, which weakens the weld. Cleaning it can prevent this. A stainless steel brush or chemical cleaner can be used for cleaning.
Next, Oh, this is another mysterious kingdom I have heard about but would never explore, just like about blood-splattered Holi cards, just like a similar ritual of playing fits and starts, where how perfectly the parts to be welded fit together plays just as critical a role in good welds. If there are holes or misaligned holes, it may cause some defect or weak weld.
Thirdly, the workspace setup ensures safety and efficiency. Proper lighting and ventilation create a comfortable working atmosphere.
Welding Parameter Adjustment
Successful GMAW Aluminum Welding has been achieved through adjusting settings. To ensure good results, voltage amperage and wire feed resemble accurate settings; otherwise, these adjusted settings ensure a stable arc and good penetration weld.
These parameters need to be monitored constantly during the welding process. They may need to be adjusted to change material thickness or welding position. Well-controlled parameters make welds stronger, cleaner, and defect-free.
Welding Techniques
GMAW aluminum welds are produced by several crucial core welding processes. One level technique is the push method, which involves pushing the light away from the weld pool. This minimizes contamination and eliminates penetration.
Controlling the rate at which the weld travels is another method. Inertia is lost in welding fast, leading to weak welds, and you can also burn through if you do it too slowly. All these techniques are practiced and help welding to make solid and clean joints.
Quality Control
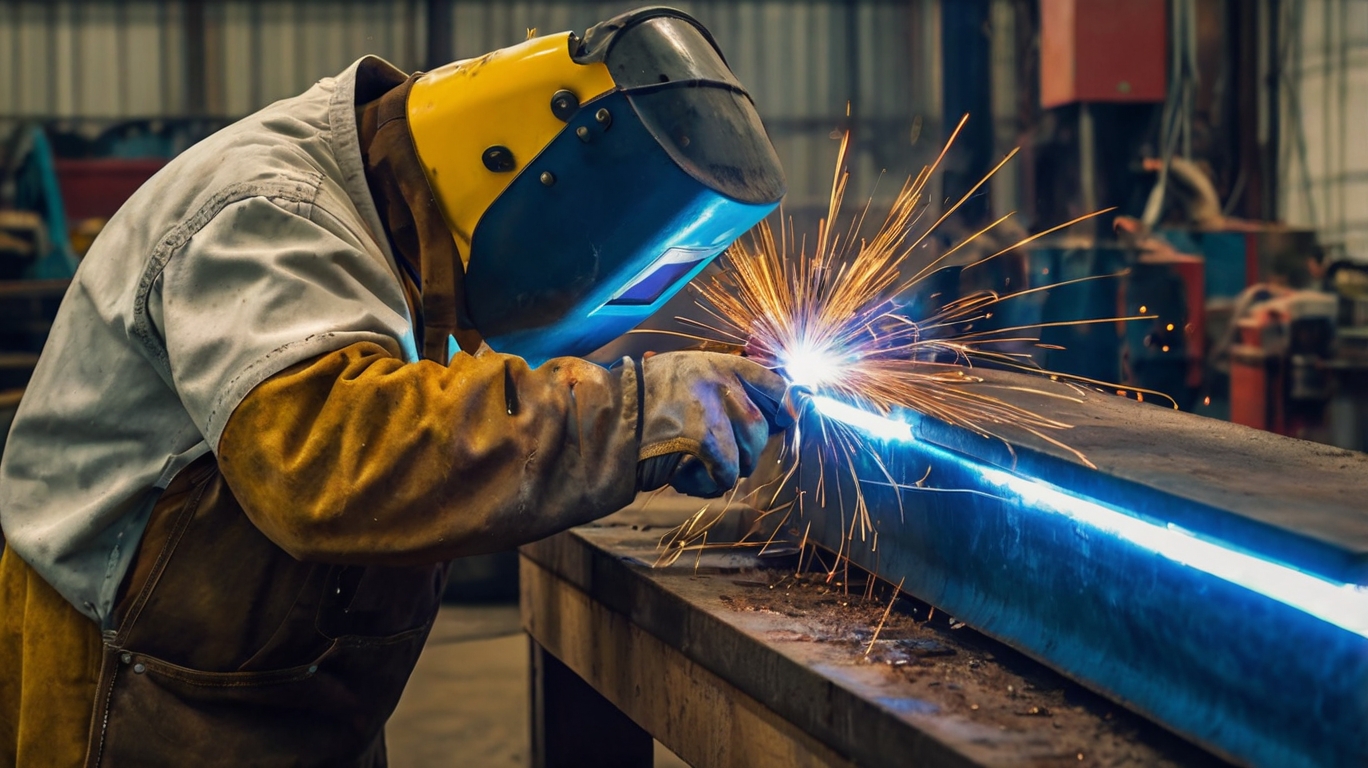
Quality control is an essential aspect of GMAW aluminum welding. It ensures that the welds are solid and reliable and involves regular inspections of welds for cracks and porosity.
Direct visual inspection after welding can detect issues early. Hidden defects can be detected by ultrasonic or X-ray testing.
This consistency ensures consistency in the welding process. This means that workers should be trained regarding such standards so they are all on the same page regarding what is required.
Quality control measures should also be checked and reviewed periodically. By staying up to date with new materials and techniques over a long period, one is assured of delivering quality work.
Frequently Asked Questions about What Gmaw Aluminum Welding is.
Q1. What is Gmaw Aluminum Welding
—A. GMAW Aluminum welding is the GMAW process used to weld Aluminum. This operation uses a continuous solid wire electrode, shielding gas, and a power source to form an electric arc that melts and connects the aluminum pieces. Because of its speed and weld quality, this technique is used in various industries, such as automotive, aerospace, and construction.
Q2. What is GMAW?
—A. GMAW refers to Gas Metal Arc Welding.
Q3. What metals can be welded with GMAW?
—A. GMAW is mainly used on Aluminum and other nonferrous metals.
Q4. Why is argon used as a shielding gas?
—A. Argon protects the weld from contamination and oxidation.
Q5. Is GMAW feasible for thin aluminum materials?
—A. Yes, but it has to be controlled carefully so as not to burn through.
Q6. What is the primary advantage of welding Aluminum with GMAW?
—A. It provides fast welding speed and clean, strong welds.
Conclusion
GMAW welding aluminum is an effective GMAW procedure for welding aluminum alloy. This process continuously feeds the wire using shielded gas to produce significant, clean welds. This method is commonly used in most industries, such as automotive and aerospaceşt.
Knowing the techniques, parameters, and materials makes all the difference in a successful weld. Good Preparation and detail produce good results. GMAW aluminum welding is still one of the most in-demand methods for speed and efficiency.
Also Read Must: