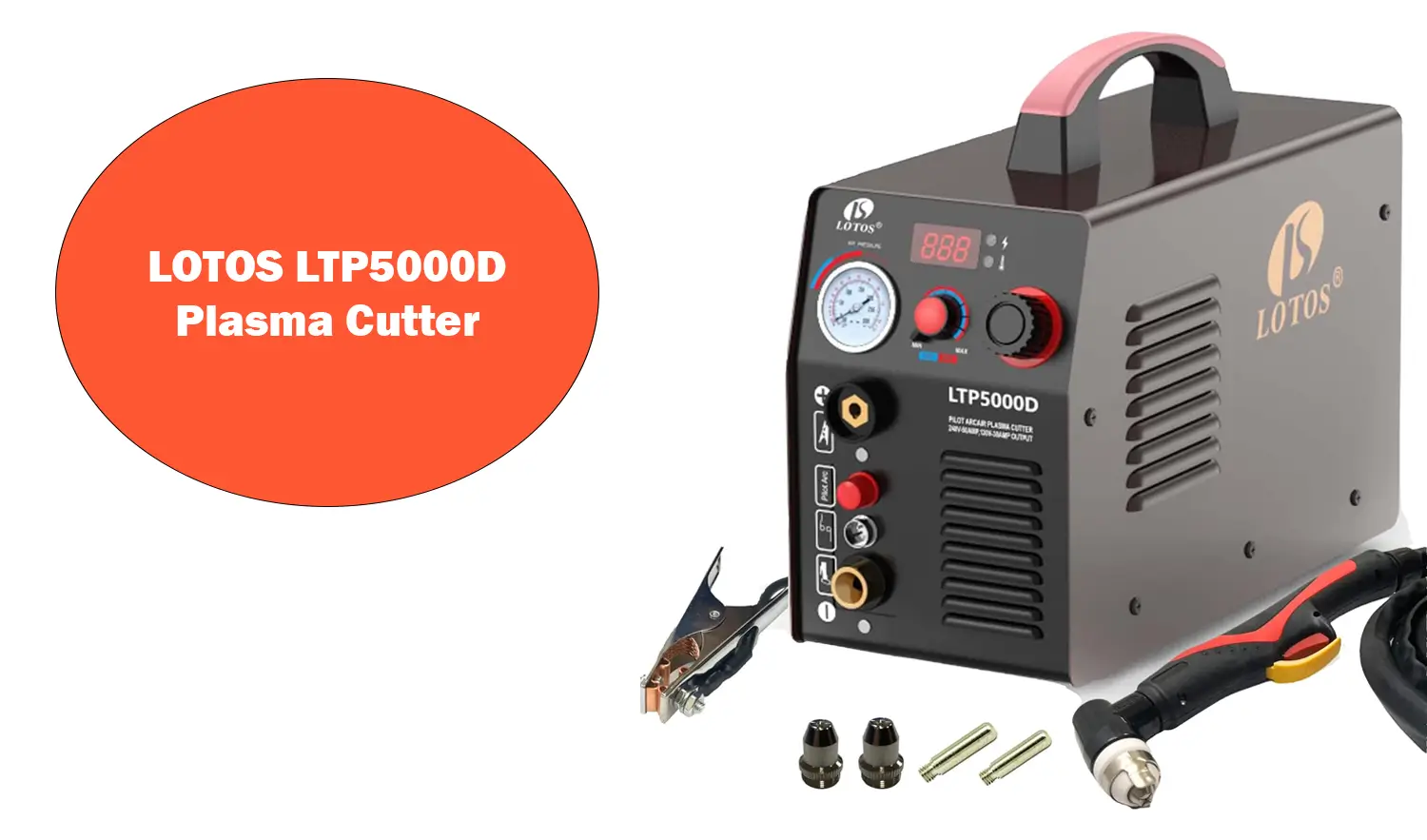
How Do Welding Helmets Work: Welding helmets and personal protective equipment (PPE) further ensure safety, such as in extreme light, heat, sparks, and dangerous ultraviolet (UV) and infrared (IR) radiation.
The welding helmet protects the eyes, face, and neck, making it an imperative rig for professional and novice welders. These helmets come with lenses that automatically darken by themselves when welding is happening, allowing you to see and keeping you protected.
Without the right welding helmet, it is common for welders not just to injure themselves: eye injuries such as “arc eye,” also known as “welder’s flash,” and other dangers inherent in the job.
They are available in different designs and include several technologies and features to accommodate multiple types of welding. So, in this deep dive, we’ll look at how these helmets work, what kinds there are, and why you should always wear one.
Welding helmets combine materials and technologies to protect the welder from harmful light, heat, and flying debris that occurs during welding. They have the shell of the helmet, the headgear, and, of course, the most important part: the lens you will look through, which may be passive or auto-darkening.
A passive welding helmet has a fixed-shade lens constructed from dark-tinted glass. Remember that this dark lens is present across the spectrum — even before you begin welding, it provides protection. However, this kind of helmet must also be lifted by welders when not welding to see their working area, and it must be dropped down again before the arc is struck.
That lens is permanently dark and protects the eyes from harmful UV and IR rays. These helmets are simple in design and typically far cheaper than their auto-darkening counterparts.
Auto-darkening helmets have a lens that detects the bright light from the welding arc and immediately darkens the lens accordingly. The lens stays crystal clear or light-smoked when no arc is present, enabling viewing without lifting the helmet.
As the arc is struck, the lens instantly darkens to protect the user’s eyes against the intense light from the arc.
Liquid crystal display (LCD) panels and light sensors make auto-darkening lenses possible.
The sensors sense the brightness of the arc and command the LCD panel to darken. The new system increases comfort and safeguards the user, particularly welders transitioning between equipment.
One constant of a helmet, whether it has a passive or auto-darkening lens, is its ability to filter out UV and IR radiation. Both lenses block 100% of these harmful rays in light or dark states. This is important because it prevents the welder’s eyes from permanently damaging.
For example, auto-darkening helmets can usually be adjusted to the appropriate shade range of the ongoing welding process. Different types of welding techniques (MIG, TIG, Stick, etc.)
also produce different brightness levels and, accordingly, require different levels of shading. Shades 9-13, for example, are used for arc welding processes, and lower shades may be adequate for less concentrated methods.
Some advanced helmets can reduce sensitivity, which controls how fast the lens darkens after detecting the arc. That is also critical when welding when the illumination may not be consistent. These settings determine how long the lens remains dark after we stop the arc so any residual light produced will not cause discomfort or damage to our sight.
A helmet shell of thermoplastic or fiberglass is heat, impact, and debris resistant. This headgear makes fitting the helmet comfortably and adequately on the welder’s head easy. Most helmets are such that they are lightweight to avoid fatigue during long welding processes.
One must wear a welding helmet as follows: The ultimate reason to wear a welding helmet is to protect your eyes from the intensity of light and radiation as they are generated by the welding arcs. Over-welding: The bright light of welding can cause photokeratitis, more commonly known as “arc eye” or “welder’s flash.” This tedious condition is caused when UV rays come in contact with the eyes, resulting in swelling of the cornea. Welding helmets solve this; they filter harmful rays, minimize exposure, and block them.
Welding generates bright light, high temperatures, sparks, and molten metal. A helmet protects a welder’s face and neck from burns and injuries from flying debris. The helmet’s shell is designed to resist these heat sources while protecting sensitive skin from hazards.
Without sufficient protection, long-term exposure to UV and IR radiation can cause cataracts, burning processes of the retina, and other serious eye diseases. A good welding helmet will ensure that these rays don’t touch your eyes, keeping your eyesight over the years. Additionally, prolonged skin exposure to UV radiation can cause- skin harm or even skin cancer, so complete coverage is crucial.
Properly sized welders can concentrate on their task- more accurately. Welders, in particular, benefit from auto-darkening helmets, which allow them to transition seamlessly between performing work and inspecting it without the need to remove and reposition the helmet multiple times. This increases efficiency and enables accurate welds in detailed or complex works.
Ergonomics and Comfort Features Of Welding Helmets Adjustable headgear and lightweight and cushioned headbands are some features that reduce welders’ fatigue and let them work without discomfort for extended periods. The other advantage of auto-darkening lenses is less neck strain from the need to flip the helmet up and down repeatedly.
Wearing a welding helmet is crucial, not only a personal preference but often a workplace rule. A helmet must comply with certain standards- established by organizations like the Occupational Safety & Health- Administration (OSHA) & the American National- Standards Institute (ANSI). These standards also help guarantee the proper protection a welder gets from welding torches.
As mentioned, passive helmets feature a fixed-shade lens, typically rated at shade 10. These helmets are ideal for welders who repeatedly perform the same type of welding and don’t need to adjust their view frequently. Although affordable, they can be less convenient for frequent work inspection tasks.
Auto-darkening helmets also have an adjustable shade level for different welding processes. When not welding, they afford a clear view while instantly darkening when an arc is sensed. They are perfect for welders who frequently switch up processes or inspect their work.
Some auto-darkening helmets use solar panels to power their lenses as a primary or supplemental power source. These helmets are efficient and eco-friendly, recharging automatically when exposed to light. They usually include backup batteries to ensure continued functionality.
Battery-powered helmets rely solely on replaceable or rechargeable batteries to power the auto-darkening lens. They are
acceptable for use in dimly lit environments or indoor settings where solar helmets might not perform as well.
Variable-shade helmets allow users to adjust the lens shade according to the welding process. These helmets are highly versatile and ideal for welders who perform different kind of welding, such as MIG, TIG, and Stick, which require different levels of protection.
For welders who value personalization, custom welding helmets offer unique designs, colors, and features. These helmets are often used to express individuality while continue safety and functionality.
Just as welding technology has made strides, so too have welding helmets. Most modern helmets have a range of features that can help provide the user safety, comfort, and efficacy. Here are some of the best features you’ll find on the high-end helmets:
All conventional welding helmets have a green or amber tint, affecting color perception. The accurate colour technology means more natural color visibility and that welders can see their space and detail where AMPOWERCYCLE is used. Not only does this improve visibility, but it also helps cut down on eye strain during longer jobs.
A workaround for this is grind mode on some helmets, which allows you to lock the lens in a light state (site shade 3 or 4)—perfect for grinding, cutting, or prepping, for example. Welders can switch between welding and non-welding applications without removing their helmets, which increases productivity.
Welding is physically intensive; long sessions can strain the neck and head. Some advanced helmets also carry adjustable headgear with cushioned pads for conformity and comfort. This allows the helmet’s weight to be redistributed more evenly, minimizing fatigue and discomfort when worn for extended periods.
Modern helmets are built with lighter materials, such as thermoplastics or composite materials, that are significantly easier to wear over a long time. While offering adequate protection, they are manageable on a welder’s neck and shoulders. This is even more important for welders who work for long periods in professional settings.
Some helmets are designed to allow welders to set the shade and sensitivity of the auto-darkening lens. That means, depending on the job and personal preference, welders can adjust their helmets to react faster or more slowly. This feature is helpful if the user often works in varying lighting conditions or uses different types of welding equipment.
Welding can create very harsh situations involving heat and flying debris. High-performance helmets utilize materials that withstand heat and impact, making them ideally suited for the rigors of a welding/ fabrication shop or construction site. They protect the welder from burns and injuries and are sturdy for long-lasting use.
Some helmets come with integrated respirators for welders working in poorly ventilated areas or around fumes or dust. The respirators themselves filter out harmful particles in the air, thus providing cleaner air to breathe. At the same time, wearing a direct-pressure respirator prolongs the welder’s life as they can work for longer periods without getting tired. This function improves the overall safety of the user.
Many newer helmets also have auto-on and auto-off functions. The helmet automatically powers on when it detects movement and/or light exposure. This keeps the auto-darkening lens always ready when needed and the helmet turned down when not in use to conserve battery life.
Each welding process presents challenges and hazards, making a welding helmet crucial for safety and performance across various welding applications.
In MIG welding, welders work with a continuously fed wire that melts and joins metals. This process generates intense arcs and requires a high level of visibility. A good auto-darkening helmet with adjustable shade levels is vital for MIG welding, as it allows the welder to see clearly during setup and provides complete protection during the welding.
TIG welding is known for producing very bright arcs, making eye protection especially important. This welding process often requires precision, and an auto-darkening helmet with true-colour technology helps welders see their workpieces in more natural colors and details. Adjusting sensitivity and delay settings is also crucial in TIG welding, which often involves lower amperage levels.
Stick welding is a more traditional welding technique that generates a considerable amount of sparks and spatter. It requires a welding helmet with excellent impact and heat resistance. Passive helmets work well for stick welding, but auto-darkening helmets provide greater convenience, especially for long projects that require multiple starts and stops.
Though not a welding process, plasma cutting also requires protection from intense light and heat. Helmets with grind mode or lower shade settings (e.g., shade 5-9) are ideal for plasma cutting, as they protect the welder’s eyes while offering enough visibility to see the cutting path.
Like MIG welding, flux-cored arc welding (FCAW) involves a constant-feed wire, creating intense heat and spatter. Welding helmets that provide high levels of shade protection, coupled with auto-darkening features, are well-suited for this process. The helmet’s durability is also important, as this technique is often used in outdoor or industrial environments.
The reaction time of a welding helmet refers to how quickly the lens darkens once an arc is struck. Faster reaction times reduce the risk of temporary eye strain and fatigue. Helmets with high-quality auto-darkening filters usually have a reaction time of 1/25,000 to 1/50,000 of a second, making them-ideal for high-frequency welding tasks.
The size of the viewing area is another critical consideration. Larger viewing areas provide more visibility, which is particularly
helpful for welders who work on complex or large projects. However, a larger viewing area may also add weight to the helmet, so welders should balance visibility and comfort.
Optical clarity ratings determine how welders can see through the lens. These ratings are based on four categories: optical class, diffusion of light, variations in luminous transmittance, and angle dependency. The best helmets have a 1/1/1/1 rating, providing excellent clarity and consistent shading across all angles without distortion.
Solar panels, batteries, or a combination can power welding helmets. Solar-powered helmets are convenient and eco-friendly, while battery-powered helmets provide consistent performance regardless of ambient light levels. Some advanced helmets offer both power options, ensuring reliable operation in any environment.
The helmet’s weight is essential for user comfort, especially during extended welding sessions. Lighter helmets lower neck strain & fatigue, which can be especially-helpful for welders who need to move around frequently or work on projects requiring long welding periods.
Welding helmets come in a wide-range of prices, depending on the features they offer. Welders should consider their needs and choose a helmet that balances cost, protection, and functionality. While premium helmets provide the most advanced features, such as auto-darkening filters, customizable settings, and accurate color technology, more affordable models can still provide adequate protection for less demanding tasks.
A high-quality welding helmet should meet or exceed safety standards set by organizations like ANSI Z87.1 and OSHA. These standards ensure the helmet protects against UV and IR radiation, impact, and heat. Helmets that comply with these standards are more reliable and provide better long-term protection for the welder.
Regular maintenance is crucial to ensure that your welding helmet provides maximum protection and performance.
The lens is essential to your helmet, and keeping it clean is vital for clear visibility. Use a soft, lint-free cloth to wipe-away dirt and debris from the lens. If your lens becomes scratched or harmed, replace it immediately to maintain optical clarity and protection. Always follow the manufacturer’s instructions when replacing lenses.
It’s essential to check the battery life regularly for helmets powered by batteries and return them as needed. Many auto-darkening helmets feature low-battery indicators, alerting you when it’s time for a replacement. If your helmet is solar-powered, make sure the solar cells are clean and exposed to enough light to keep the batteries charged.
Headgear can wear out over time, affecting the helmet’s fit and comfort. Periodically check the headgear for signs of wear, such as fraying straps or weakened adapt-mechanisms. Replace any worn-out part to makesure the helmet fits securely and comfortably.
The helmet’s shell should be free of cracks, dents, or other harm that could compromise its ability to protect against heat and impact. If you notice any damage to the shell, consider replacing the helmet, as it may no longer provide adequate protection.
Store your welding helmet in a cool, dry place away from direct sunlight & harsh chemicals when not in use. Prolonged submission to heat or UV rays can degrade the helmet’s materials, reducing its effectiveness over time.
Arc sensors are critical in modern welding helmets, particularly those with auto-darkening technology. These sensors detect- the arc’s intensity and trigger the lens to dim within milliseconds, protecting the welder’s eyes from harmful light & radiation. The number of arc sensors in a helmet typically ranges from two to four, with more sensors offering better coverage and sensitivity. Here’s why arc sensors are essential and how they function in various welding scenarios.
Helmets with four arc sensors provide superior coverage compared to models with only two. When welding in awkward positions or when part of the arc is obstructed, helmets with fewer sensors may fail to detect the arc properly, leading to delayed lens darkening. Four sensors help ensure the helmet responds instantly to the arc, even in tight spots or when welding at odd angles.
Arc sensors allow the welder to adjust the helmet’s sensitivity to match the environment or specific welding process. In low-light conditions or when working with lower amperages, the welder can increase the sensitivity to ensure that the lens darkens even with less intense arcs. Conversely, lowering the sensitivity in bright environments or high-amperage applications prevents the helmet from overreacting to other light sources.
One of the primary benefits of arc sensors is the prevention of eye fatigue and flash burns, both caused by prolonged exposure to the bright light of the welding arc. Auto-darkening helmets with arc sensors reduce the risk of these injuries by ensuring the welder’s eyes are constantly protected from the intense sunlight, UV, and infrared radiation emitted during welding.
The reaction time of a welding helmet’s lens is directly tied to the performance of its arc sensors. High-quality arc sensors can detect changes in light and darken the lens in as little as 1/25,000 of a second. Faster reaction times are essential for welders working in high-frequency applications, such as TIG welding, where even a slight delay in lens darkening can result in eye discomfort or damage.
Welding helmets with advanced arc sensors are designed to minimize false triggers caused by surrounding light sources, such as other welding arcs, sunlight, or overhead lighting. This feature is handy in busy workshops where multiple welding tasks are carried out simultaneously. Helmets with high-quality sensors distinguish between the welder’s arc and other light sources, reducing unnecessary lens darkening.
Welding helmets are designed to stalk and to and ort during long working hours. Ergonomic design plays a significant role in reducing fatigue and enhancing productivity. Let’s dive into thexploreects of helmet design and how they impact the overall welding experience.
The weight distribution of a welding helmet affects how comfortable it feels during extended periods of use. Helmets with poor weight balance can strain the neck and shoulders, leading to discomfort and reduced efficiency. High-end helmets are designed with evenly distributed weight, which minimizes the strain on the welder’s body and allows for longer, more comfortable sessions without frequent breaks.
Properly fitting headgear is essential for comfort and safety. Most modern welding helmets come with fully adjustable headgear, allowing welders to fine-tune the fit according to their head size & shape. Features such as adjustable straps, pivot points, and sweatbands contribute to a customized, snug fit that prevents the helmet from shifting or slipping during work.
Lightweight materials and thoughtful design can reduce neck strain. Welders often need to flip their helmets up and down repeatedly, and heavier helmets can cause significant neck fatigue. Helmets made from advanced composite materials like carbon fiber are strong, durable, and lightweight, making them easier to wear for prolonged periods.
Welding can generate a lot of heat, and without proper airflow, welders may find themselves overheating, mainly when working in confined spaces. Some helmets feature ventilation channels that allow for better airflow, keeping the welder cooler and more comfortable. In addition, helmets equipped with integrated respirators- provide filtered airflow, ensuring welders can breathe safely while avoiding fumes and dust.
Some helmets come with a flip-up visor, allowing welders to easily switch between welding and inspection work without removing the entire helmet. This feature is incredibly convenient when working on intricate projects that require frequent switching between welding and precision adjustments. Flip-up visors also reduce downtime, as welders can quickly assess their work without removing and repositioning their helmets.
Welding helmets must withstand various hazards in the workshop, including flying debris, sparks, and heat. Helmets made from impact-resistant materials like polycarbonate or fiberglass makesure the helmet can endure harsh working conditions. Durability is crucial, especially for welders who work in heavy industrial environments, where helmets are subject to frequent wear and tear.
While the color of a welding helmet might seem minor, it can affect how visible the welder is to others in the workspace. Brightly colored helmets or those with reflective surfaces improve visibility, reducing the chances of accidents in busy environments where multiple workers are present. Some welders also prefer custom designs or finishes for aesthetic reasons and to stand out in the workplace.
Technology for welding helmets has advanced dramatically, from bare hand-held shields to advanced auto-darkening helmets with built-in safety features. Learning more about this evolution offers insight into how modern helmets are constructed to increase welders’ safety and comfort.
The earliest form of welding protection was old manual shields, a darkened blanket that welders held up before their eyes. While these shields served an important purpose, the welder needed to use one hand to hold them up, restricting him from effectively doing his job. With technological advancements, fixed shade helmets became popular, giving the welder full use of both hands while shielding their eyes from the arc.
Auto-darkening helmets changed the game for welders. These helmets are also called auto-darkening helmets, as the lens automatically adjusts in the shade about the arc, giving you immediate protection without you having to flip the helmet up and down. This drastically increased welder productivity and safety because welders no longer had to (1) remove the helmet for setup or risk exposure to harmful light.
The earliest auto-darkening helmets were powered directly by solar energy, using ambient light to power the lens adjustment mechanism. Solar-powered helmets remain popular, but battery-powered models have exploded due to improved performance, even in low-light situations. Combining solar cells and batteries to prevent this inconsistency, hybrid power sources are now available in some helmets.
In addition, accurate color technology was developed, which enables welders to see workpieces more closely to their actual colors. This technology will not only minimize the strain on the eyes but also help welders work with more accuracy. Modern lenses generally have higher optical clarity ratings, which means they distort less and provide a clearer view from all angles.
As intelligent technology has gained traction, welding helmets have added features such as auto-on/auto-off, Bluetooth functionality, and heads-up displays (HUDs) that share real-time information with the welder. Such complex yet useful inventions make welding more straightforward, effective, and efficient, allowing for less complicated workflows and more control of the surrounding areas.
To summarize, welding helmets have become an integral part of welding as they protect the welder & help improve the welding experience.
These helmets range from the most primitive bare hand-held shields to modern auto-darkening helmets designed with advanced technologies for enhanced comfort and safety.
Arc sensors, ergonomics, impact-resistant materials, and accurate color technology — helmet technology has come a long way, providing welders with better visibility, lower strain on the eyes, and more flexibility under different working conditions.
When looking for the most appropriate welding helmet, you need to pay attention to many different features like weight, adjustability, sensitivity, and clarity of the lens, and also consider the type of welding being done.
Investing in a-high-quality helmet that fits well, is durable, and has high-tech features can improve uptime and minimize fatigue — but, most importantly, it prevents exposure to dangerous hazards like UV and IR radiation, debris, and heat.
—A. Auto-darkening helmets adjust the shade of the lens automatically when the welding arc is detected. This feature protects the welder’s eyes from harmful ultraviolet (UV) and infrared (IR) radiation while allowing them to see their work clearly when the arc is inactive.
—A. Auto-darkening helmets provide more convenience and safety. They eliminate the need to flip the helmet up and down between welding sessions, allowing for uninterrupted work and reducing neck strain. They also offer more control over the lens shade, improving visibility and precision during different types of welding.
—A. The appropriate shade depends on the welding type and the arc’s intensity. Most auto-darkening helmets come with adjustable shade settings that range from #8 to #13. Lower numbers are for low-amperage welding, and higher numbers are for brighter, high-amperage welding processes like MIG and TIG welding.
—A. Accurate color lenses enhance visibility by reducing the green tint in traditional welding helmets. This allows welders to see more clearly, improving the precision of their work and reducing eye strain over extended periods.
—A. Auto-darkening lenses can last several years, depending on usage, exposure, and care. High-quality helmets with replaceable batteries may have a longer lifespan. Keeping the helmet clean and storing it properly also helps prolong the life of the lens.
—A. Yes, most modern welding helmets have enough space to accommodate prescription glasses. Some helmets also offer magnifying or “cheater lenses” as an alternative for welders needing vision correction.
At Best Welder Reviews, Hamim Minhas has years of welding experience and expertise in evaluating welding tools and accessories. My goal is to provide clear, reliable and deep insights to help welders of all levels make informed decisions. Whether you're a beginner or an expert, my thorough reviews, buying guides, and tips ensure you find the right tool for every welding project.
Copyright © 2025 Best Welder Review. All rights reserved.