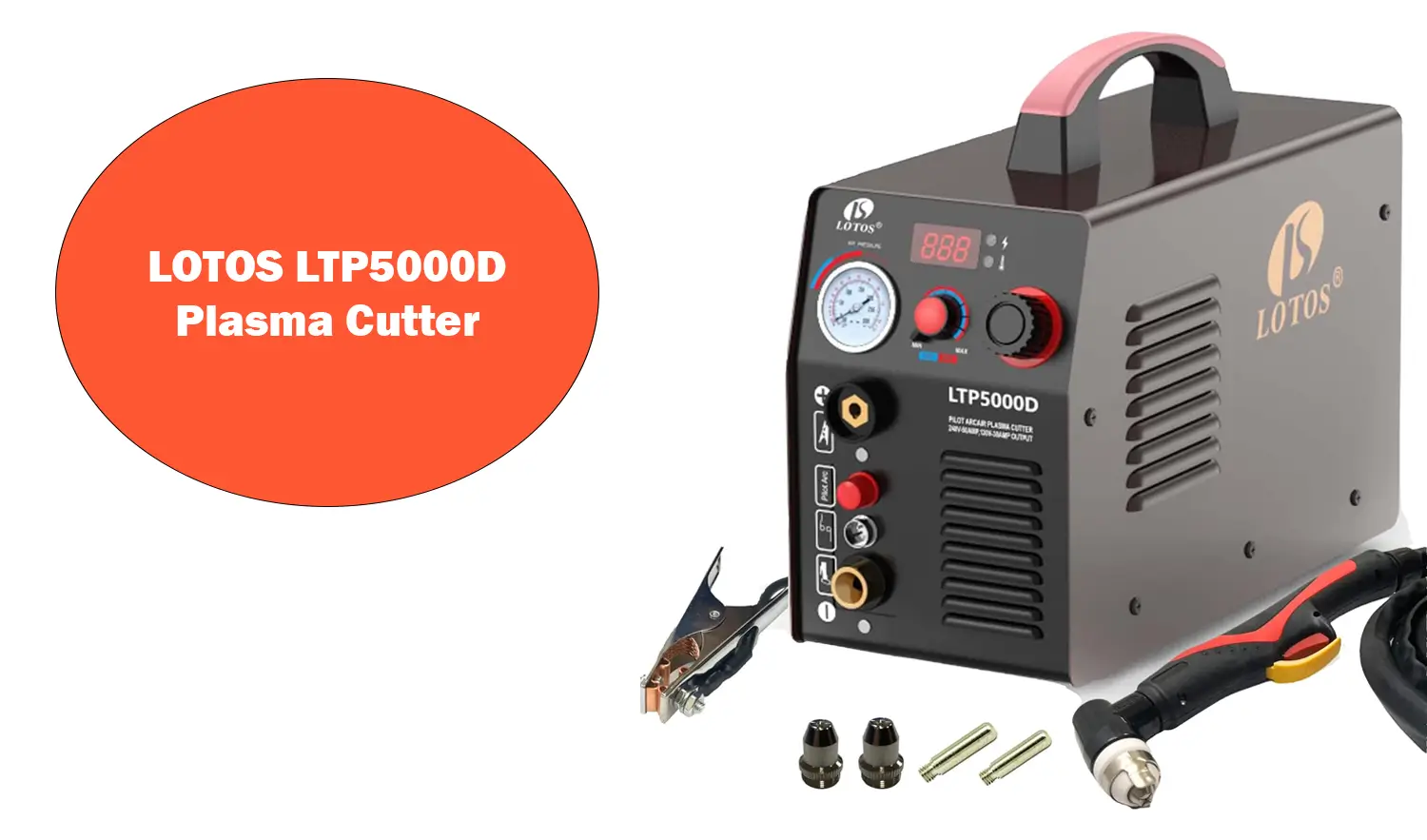
MIG welding is a process that joins metal pieces using an electrical current to melt a consumable wire, which serves as both the electrode and the filler material to fuse the metals. This technique is called gas metal arc welding (GMAW) or wire welding.
In contrast to tungsten inert gas (TIG) welding, which uses a tungsten electrode to heat and join metal surfaces directly. In this blog, we explore frequently asked questions such as “What is MIG welding?” and discuss the pros or cons of this welding process.
MIG Welder operates a constant voltage authority supply to complete an electric arc that dissolves and fuses the base metal with a continually fed filler wire. At the same time, an inert shielding gas is delivered through the torch to protect the weld pool from atmospheric contamination, as inert gases do not react with the filler or the weld pool.
This welding technique is commonly employed for heavy-duty fabrication projects like metal gates. MIG welding is faster than TIG welding, resulting in quicker lead times and diminished production costs. Additionally, it is easier to master and produces welds that often require little to no post-weld cleaning and finishing. Despite these advantages, TIG welding is still preferred for tasks requiring highly precise, strong, and exceptionally clean welds.
The MIG welding process is based on forming an electric arc between a consumable wire electrode and the workpiece. This electric arc generates intense heat, which melts the wire and the workpiece, allowing it to fuse. The wire electrode is fed continuously through the welding gun, maintaining a consistent arc and allowing for continuous welding without stopping to replace the electrode.
The critical components of the MIG welding process are:
MIG welding offers several advantages, making it a preferred choice for many welding applications:
MIG welding is widely utilized in various drives due to its versatility and efficiency. Some typical applications include:
The wire electrode is a crucial component in MIG welding, acting as both the electrode and filler material. The choice of wire electrode depends on the type of base material being welded and the specific application. Common materials used for wire electrodes include:
Inert gases are used in MIG welding to protect the weld pool from atmospheric contamination. The choice of shielding gas influences the weld quality, penetration, and overall welding characteristics. Common inert gases and gas mixtures used in MIG welding include:
The welding torch, or gun, is essential in MIG welding, directing the wire electrode and shielding gas to the weld pool. Critical materials used in welding torches include:
The power source in MIG welding provides the necessary electrical power to create and support the arc. Critical materials and components used in power sources include:
The equipment and consumables used in MIG welding play a crucial function in specifying the quality and efficiency of the welding process. Key components include:
MIG welding can employ techniques to achieve specific weld characteristics and meet various application requirements. Some standard methods include:
Safety is critical to MIG welding, as the process involves high temperatures, electrical currents, and hazardous fumes. Key safety considerations include:
MIG (Metal Inert Gas) welding uses a consumable wire electrode and a fixed or semi-inert gas to protect the weld pool, making it suitable for various materials and applications. TIG (Tungsten Inert Gas) welding utilizes a non-consumable tungsten electrode and a fixed gas, typically argon, providing precise control over the weld. It is often used for thinner materials and high-quality welds.
MIG welding can be challenging outdoors because wind can disperse the shielding gas, contaminating the weld pool. To mitigate this, windshields or flux-cored wire with self-shielding capabilities can be used.
The choice of wire electrode depends on the base material, thickness, and welding position. ER70S-6 is a common choice for carbon steel. Options like ER308L or ER316L are used for stainless steel. ER4043 or ER5356 is famous for aluminum. Consider the manufacturer’s recommendations and your project’s specific requirements.
Shielding gas protects the molten weld pool from atmospheric contamination, preventing oxidation and other defects. It helps stabilize the arc, improve bead appearance, and influence penetration and spatter levels.
To reduce spatter, ensure proper welding parameters, such as voltage and wire feed speed, are set correctly. Use high-quality shielding gas and maintain a consistent stick-out distance. Clean the workpiece thoroughly before welding and use anti-spatter spray if necessary.
MIG welding can be functioned in various places, including flat, horizontal, vertical, and overhead. However, the flat position is the easiest and most common, providing reasonable control and visibility of the weld pool.
To prevent porosity, ensure proper gas flow, clean the workpiece thoroughly, and avoid excessive travel speed. Use the correct filler material to prevent cracking, preheat the workpiece if necessary, and control cooling rates.
MIG welding can join some dissimilar metals but requires careful wire electrode selection and shielding gas selection. Compatibility and metallurgical properties must be considered to avoid cracking or poor weld quality.
MIG welding is a universal and efficient welding technique widely used in various industries for its ability to produce high-quality welds with minimal post-weld cleaning. Understanding the principles, equipment, methods, and safety considerations of MIG welding is essential for achieving successful welding outcomes and maintaining a safe working environment. Whether used in automotive, construction, manufacturing, or aerospace applications, MIG welding remains a valuable tool for joining metals in various projects.
At Best Welder Reviews, Hamim Minhas has years of welding experience and expertise in evaluating welding tools and accessories. My goal is to provide clear, reliable and deep insights to help welders of all levels make informed decisions. Whether you're a beginner or an expert, my thorough reviews, buying guides, and tips ensure you find the right tool for every welding project.
Copyright © 2025 Best Welder Review. All rights reserved.